事業案内 SERVICE
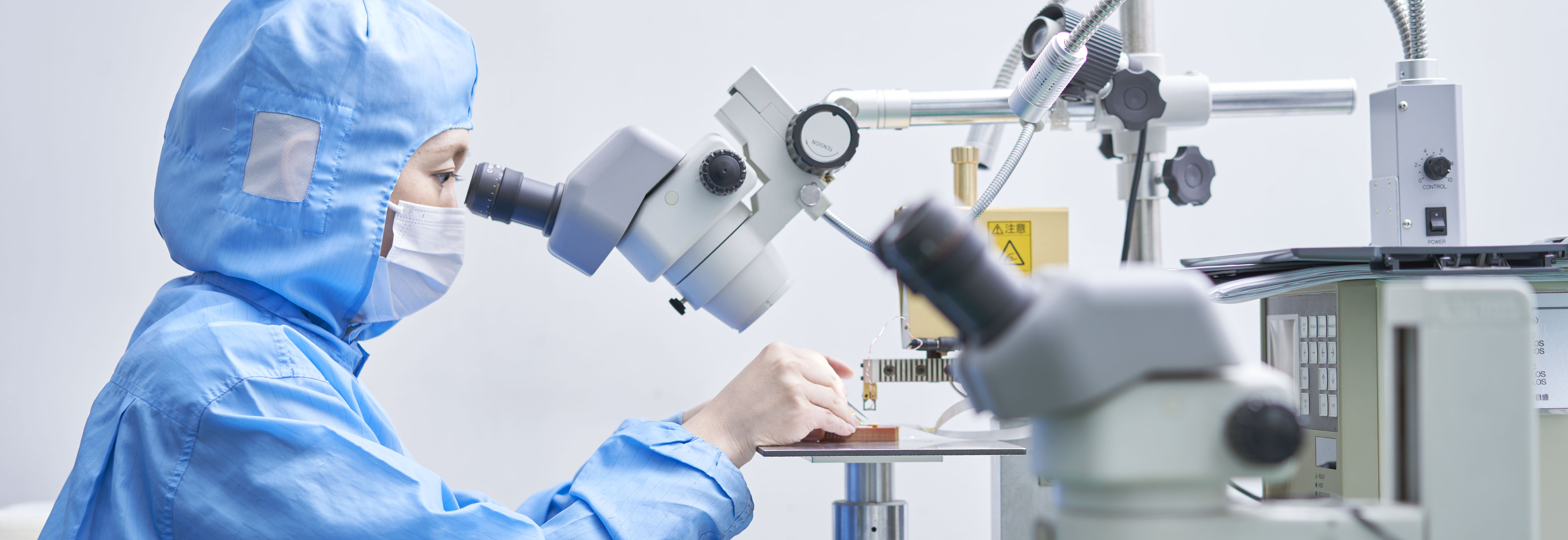
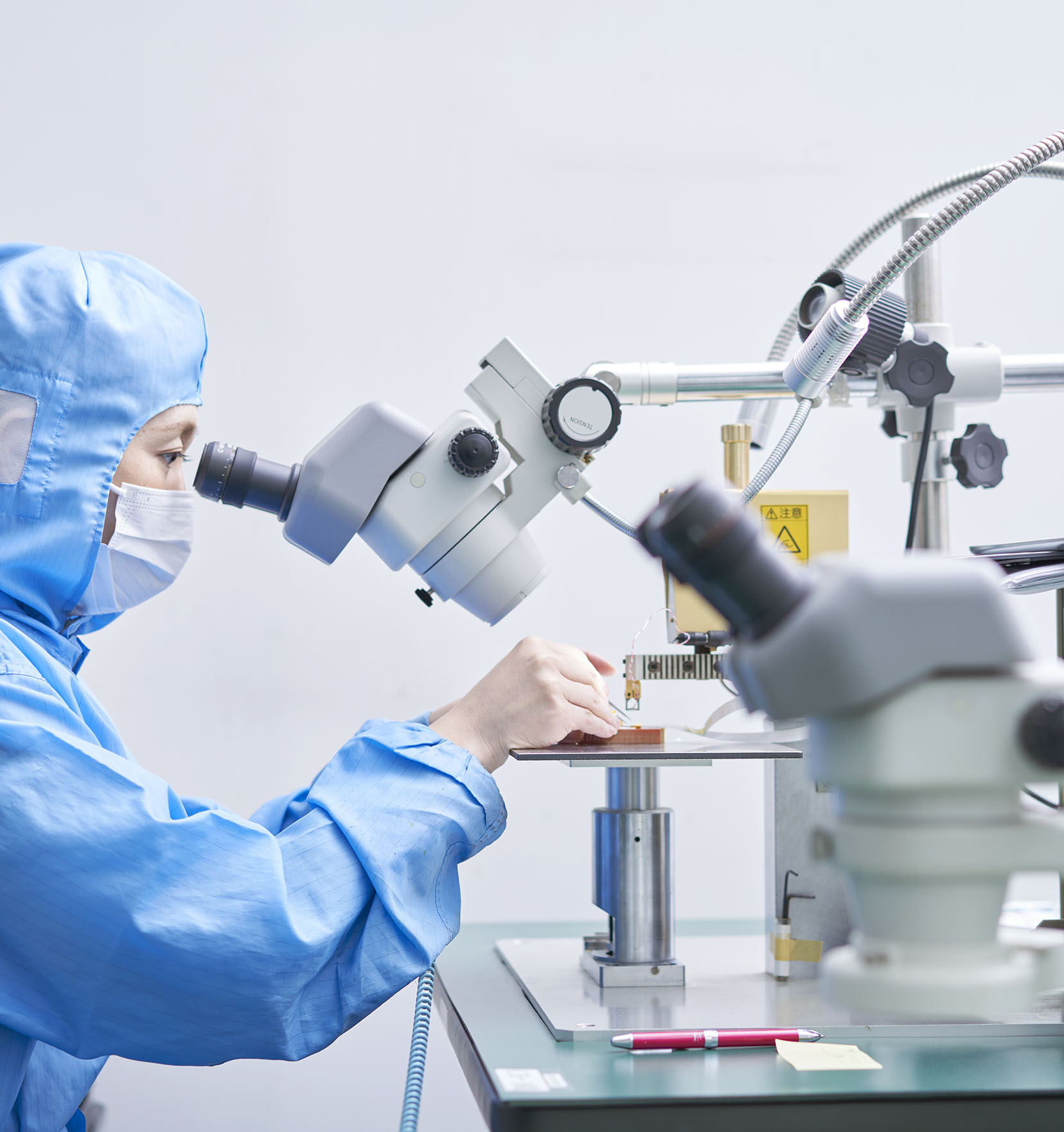
基板実装
各種プリント基板の組立・製造
最新設備と独自ノウハウで 唯一無二の高みに プリント基板へのパーツ実装作業では、自動化・機械化の不可能な分野こそプロシードの技術の見せ所です。職人の優れた技術と最新装置の運用を両輪に、他社にはできない高品質な実装を提供します。特に大型多層基板においては、最新装置の運用と手動実装の両面において、プロシードならではの技術と経験が蓄積。外観検査装置と目視検査支援機による検査も合わせて、電子機器に必須となる信頼性を高い次元で担保します。また、小型基板において印刷マスクの製作から実装までを自社内で完結するほか、「伝統的な職人気質」による完全手作業の特殊実装にも対応。多品種・小ロット生産や試作のようなニーズにも、短納期での対応が可能です。
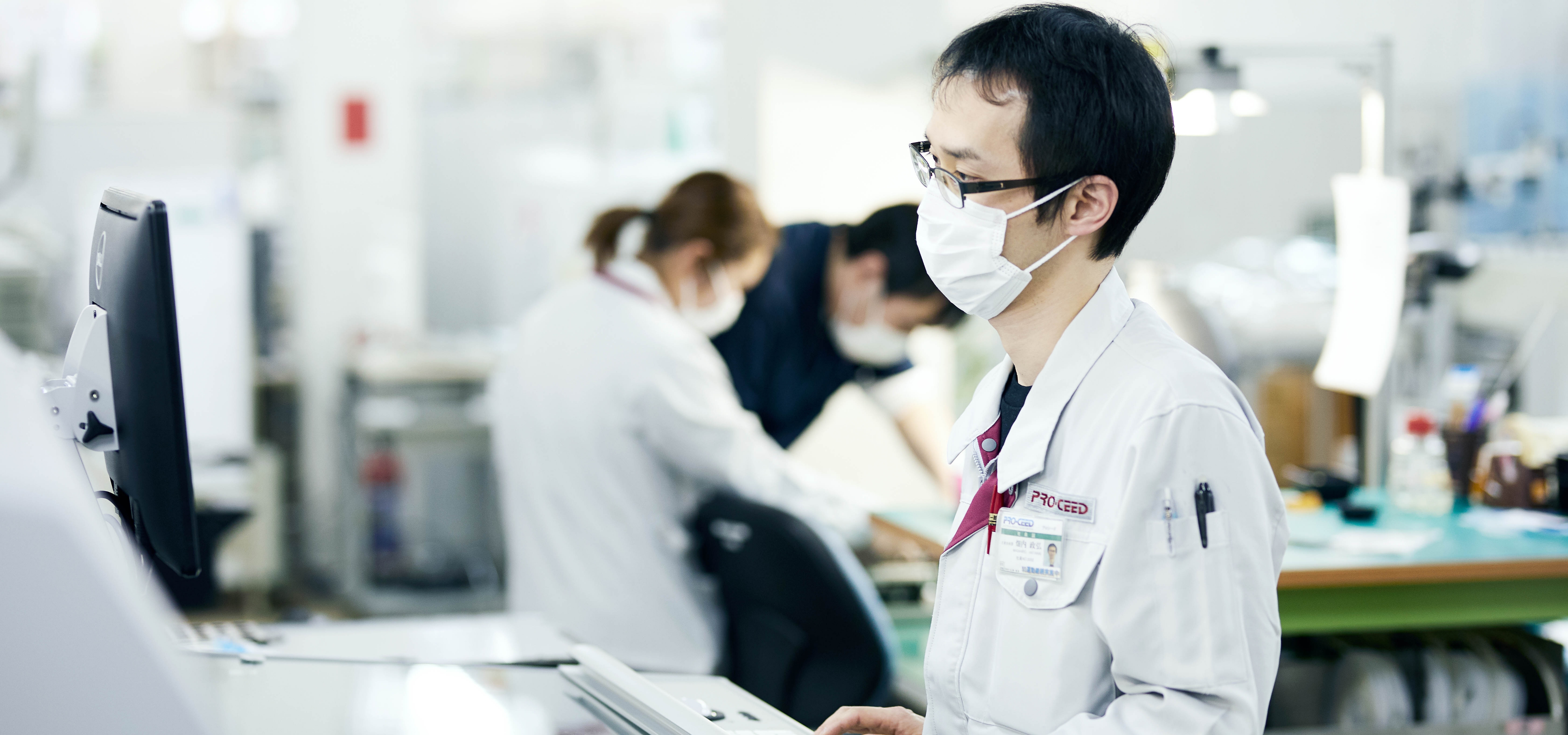
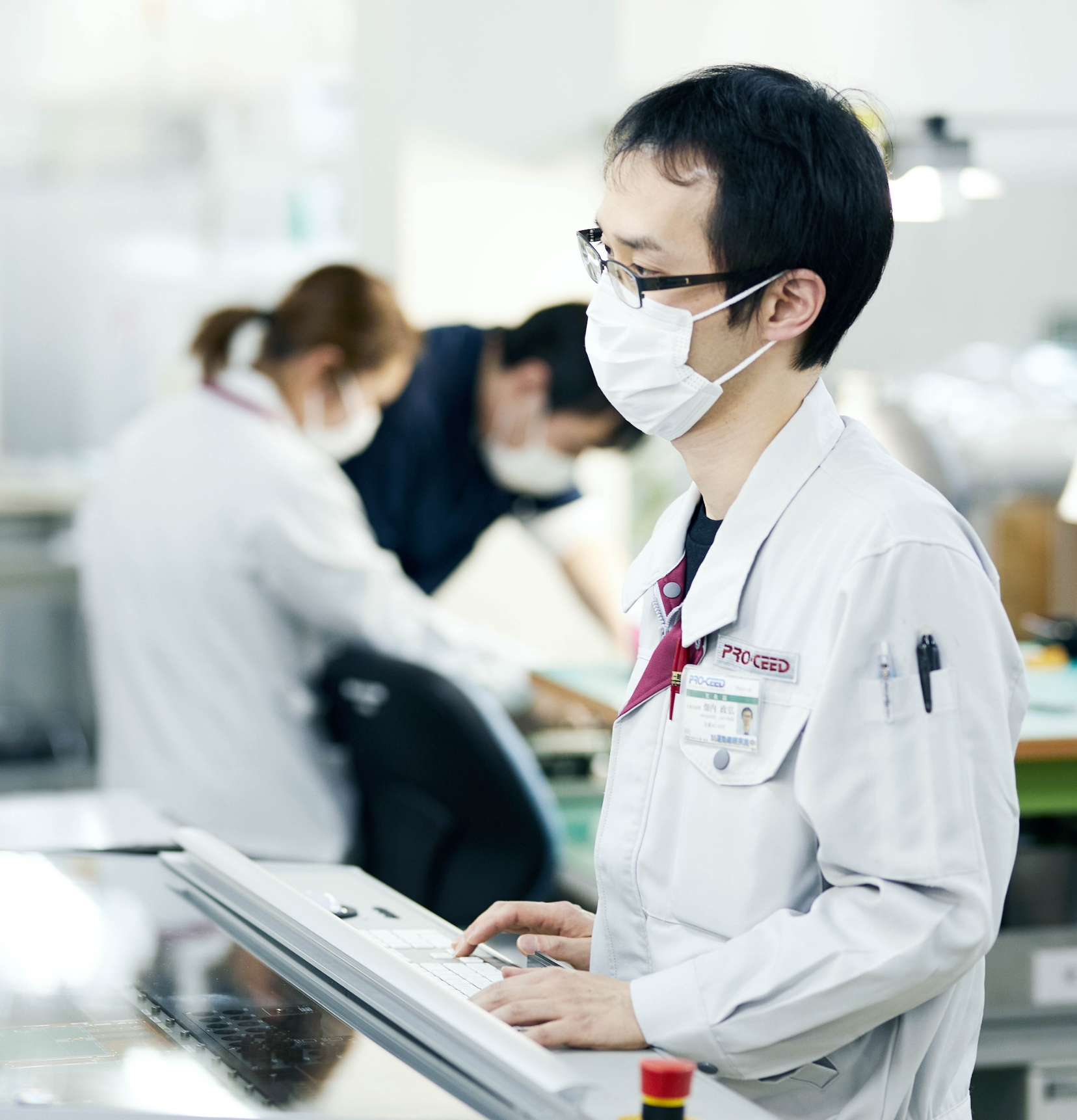
手作業と自動実装の
どちらも最高品質です
プロシードにおける基板実装作業は、「最新の自動装置による実装」「職人の手作業による実装」「印刷マスクによる実装」の3つに大きく分けられます。いずれも、他社にはない技術とノウハウの蓄積が自慢です。
最新の自動装置
職人の手作業
印刷マスク
主な実装事例
最新の各種実装関連装置により、高密度かつ微小なパッケージをフォロー。部品調達コストの低減と短納期を実現します。リフローは鉛フリー半田に適した強制熱風対流方式を採用し、窒素(N2)にも対応。本システムにより、最大で609×914mmもの大型多層基板への、迅速かつ正確な実装が可能です。
使用機材
- マウンター
- MYCRONIC MY200SX-14/T6
- リフロー
- 千住金属 SNR-1465GT-S
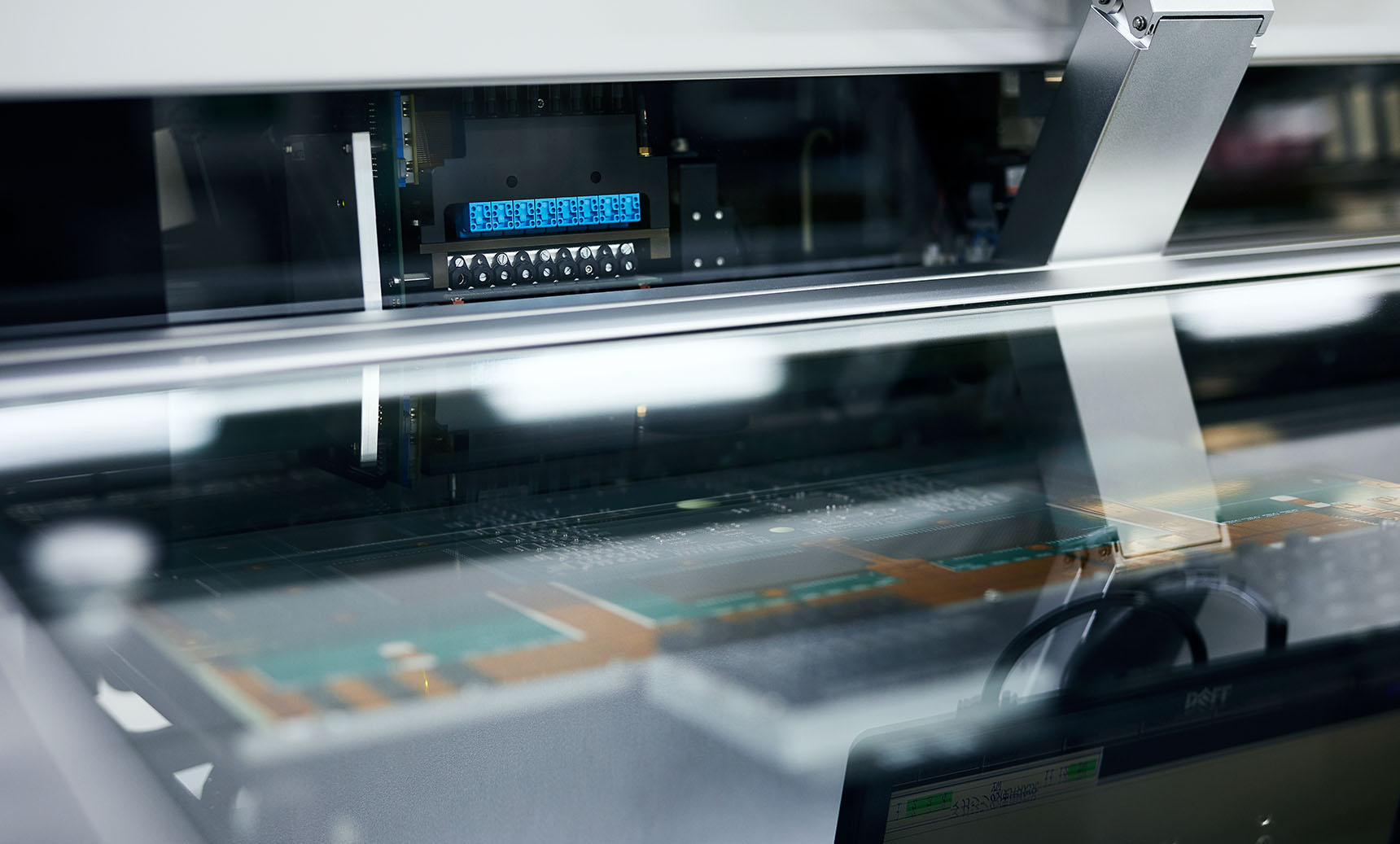
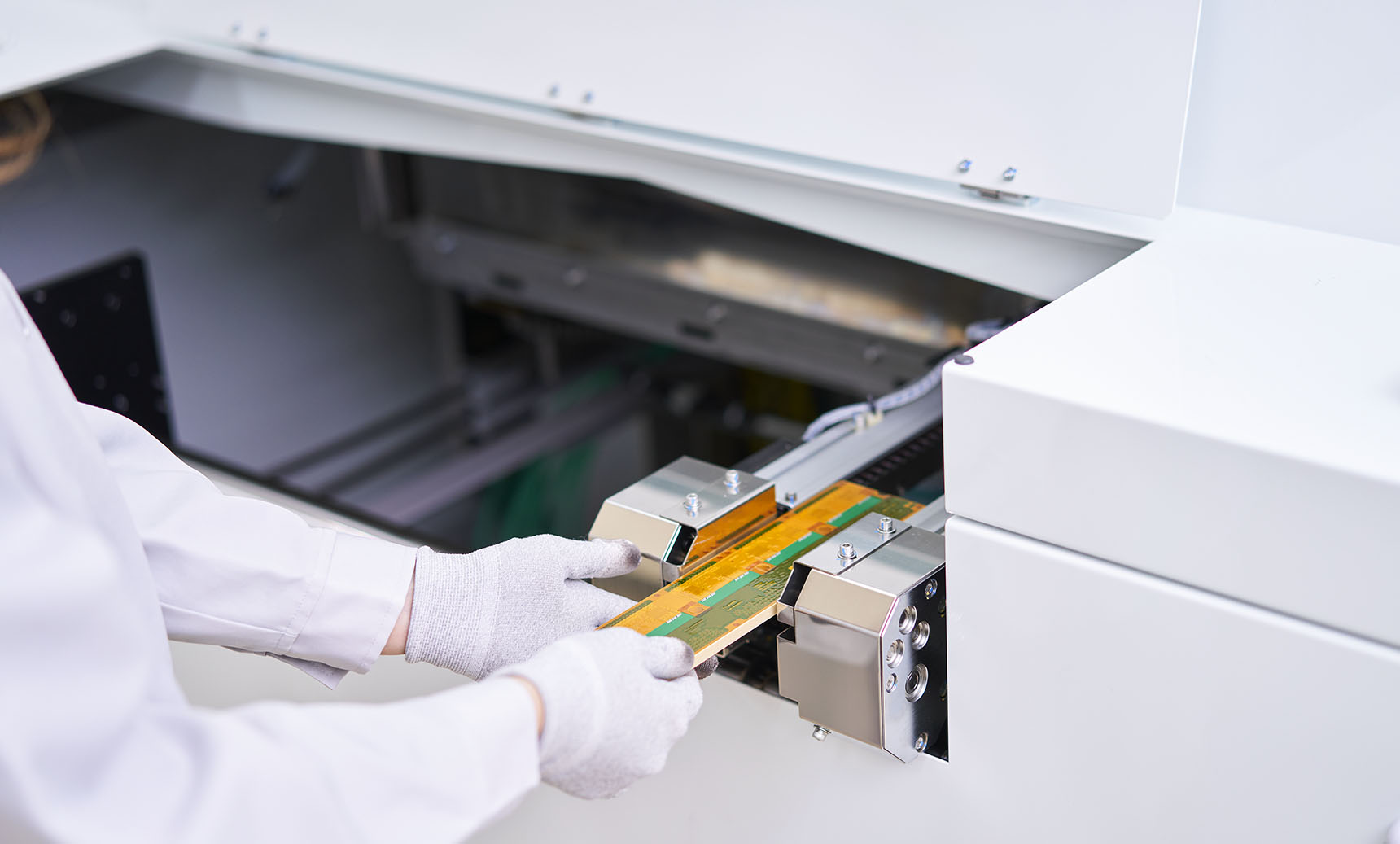
職人の技術による部品実装&目視検査
最新装置に勝るとも劣らない職人の技術により、マウンターで実装できない部品の手作業による実装や、特殊実装に対応します。加えて、ダブルカメラを備えた支援機を用いる精密な目視検査も実行。高品質と短納期を両立します。
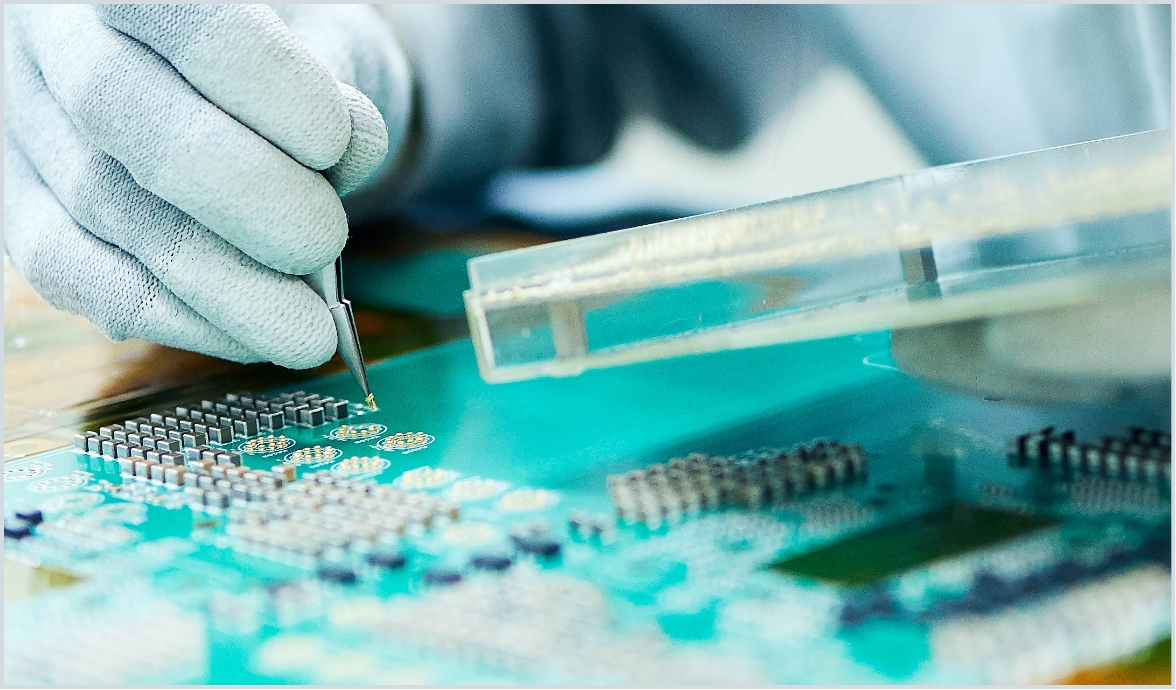
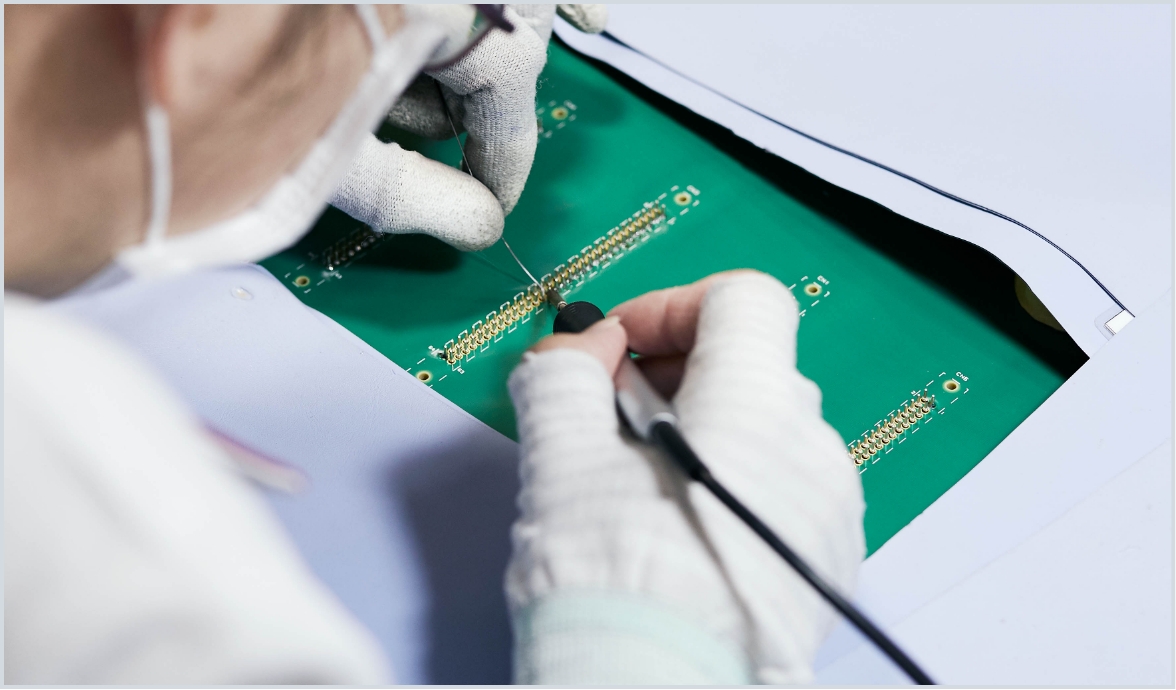
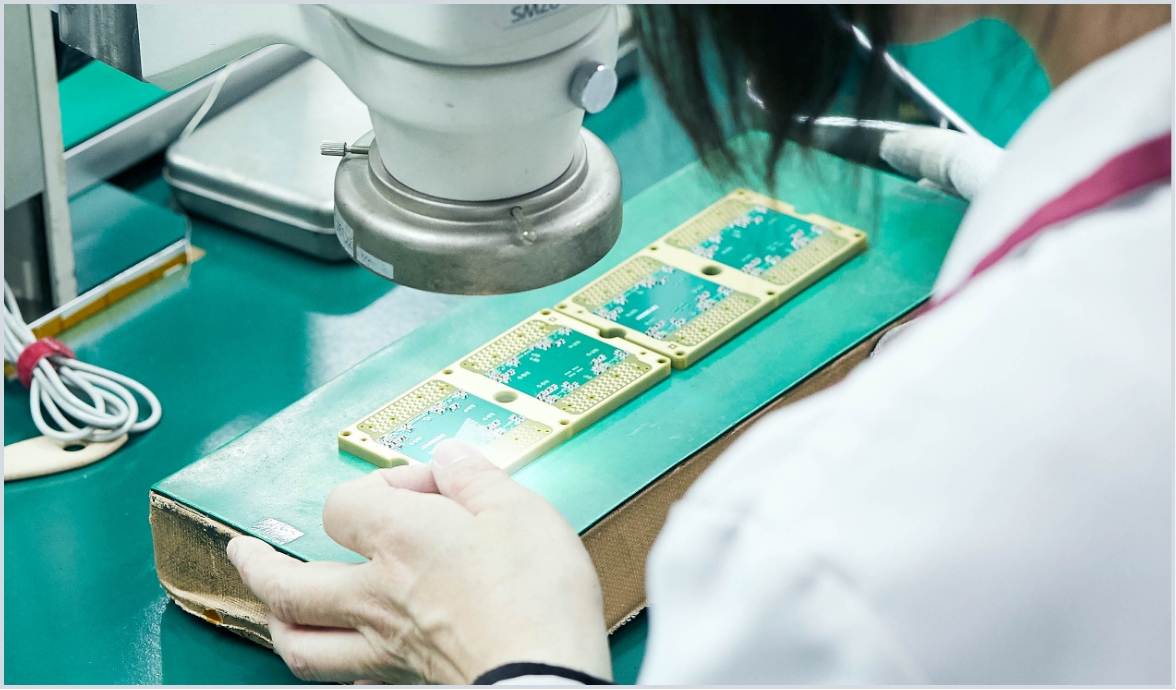
印刷マスクの製作
CADやDXFなどのデータをいただければ、小型切削加工機により社内で印刷マスクを製作します。これにより、最新の半田印刷ジェットプリンタを使うまでもない小規模な基板においても、安価で迅速かつ高品質な実装を実現しています。
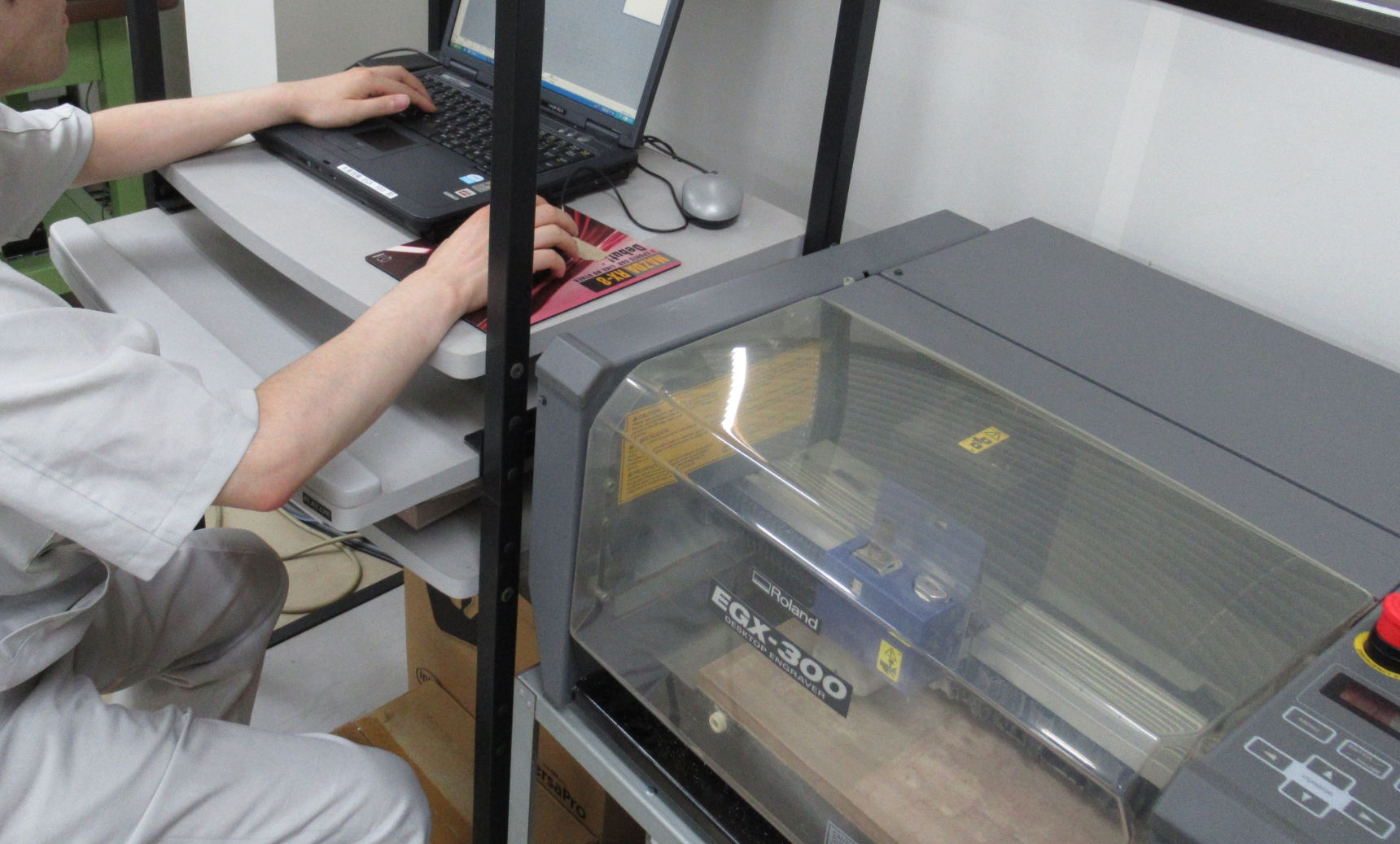
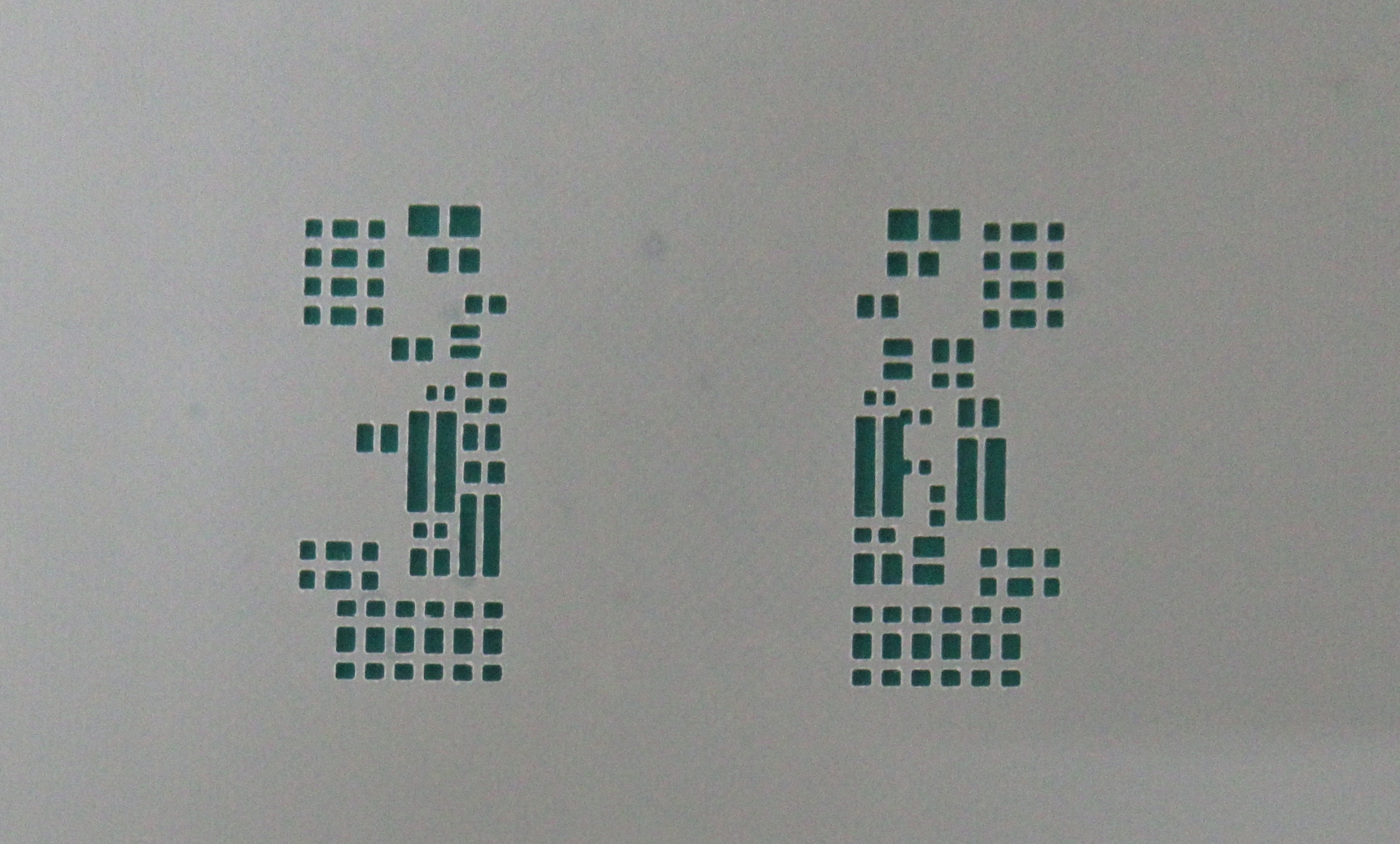
組立電装
電装機器の組立・製造
気の遠くなるような作業も 一歩一歩着実に 電装機器の組立と製造にも、プロシードの技術は生きています。微細な半田付けは言うに及ばず、数千単位のケーブル配線やプローブピンの挿入といった途方もない作業も、すべて職人の手によって手作業で完遂。さらには検査も手作業で行い、機械では判別が難しい微妙な差異をも判定して、クライアントが求める水準の製品を確実に作り上げます。加えて、治工具の内製化や組配作業の効率化により、スピーディーな納品も実現。クライアントのニーズにマッチした「高品質」「高精度」「低コスト」な組立電装サービスを提供しています。
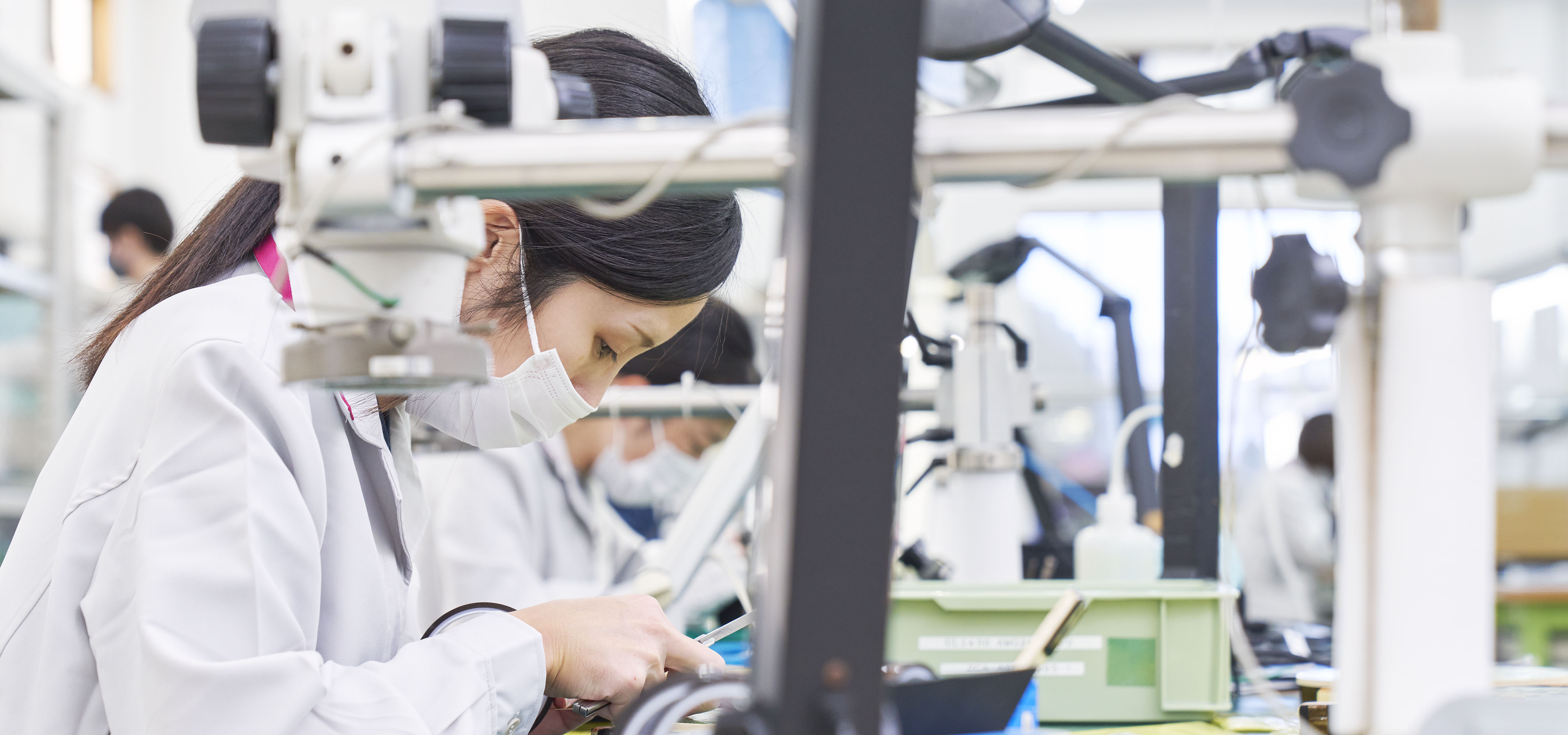
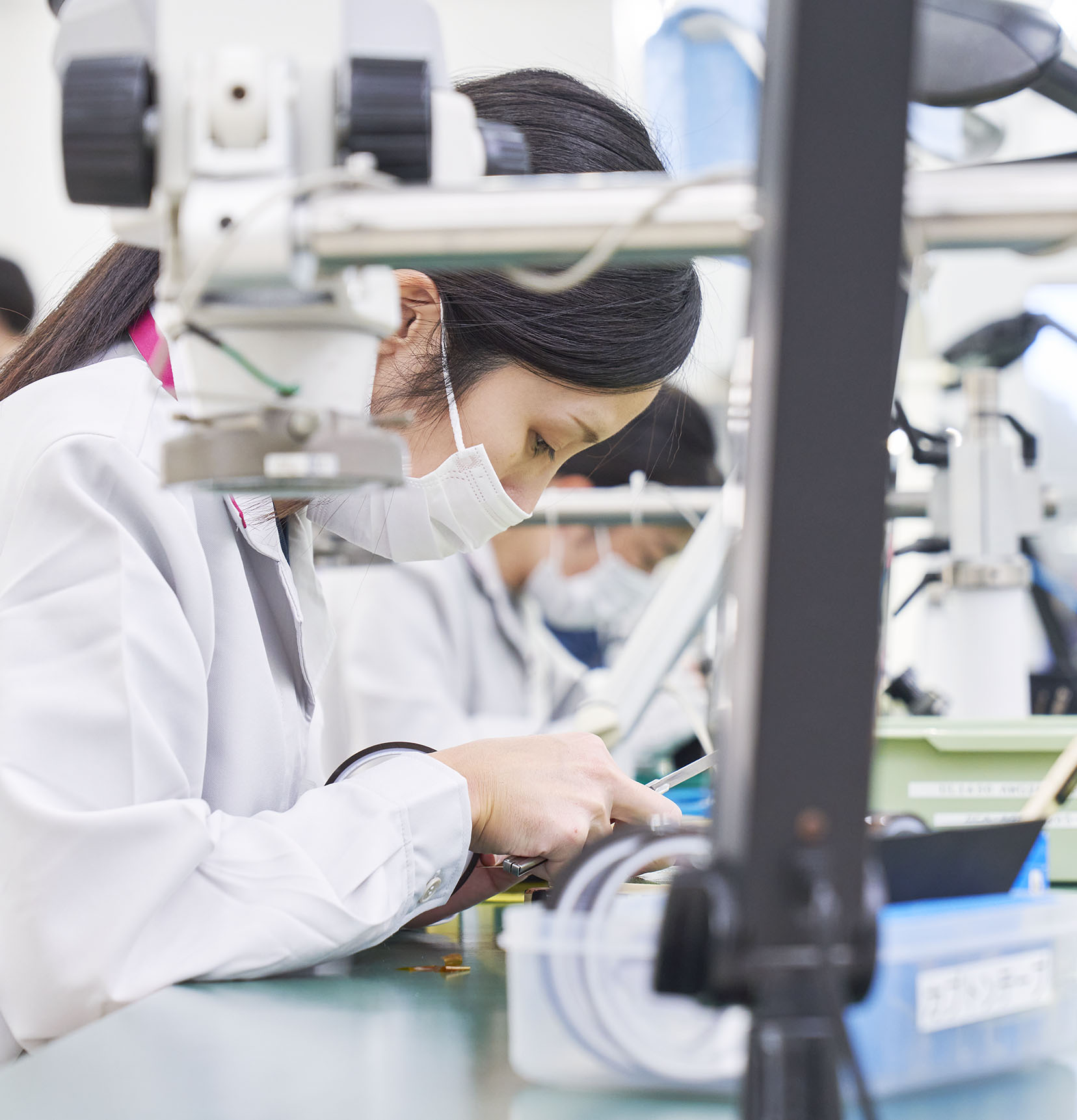
組立電装の工程例を
ご覧ください
プロシードにおける基板実装作業は、「最新の自動装置による実装」「職人の手作業による実装」「印刷マスクによる実装」の3つに大きく分けられます。いずれも、他社にはない技術とノウハウの蓄積が自慢です。
組立作業
導通検査
組立完了
手順1:組立作業
あらかじめ整形しておいたケーブルを200枚強の子マザーボードに配線した後、誤配に気をつけながら親マザーボードにも配線し、仮組み。組立は、ケーブルにストレスを与えないように考慮された作業手順にそって行われます。
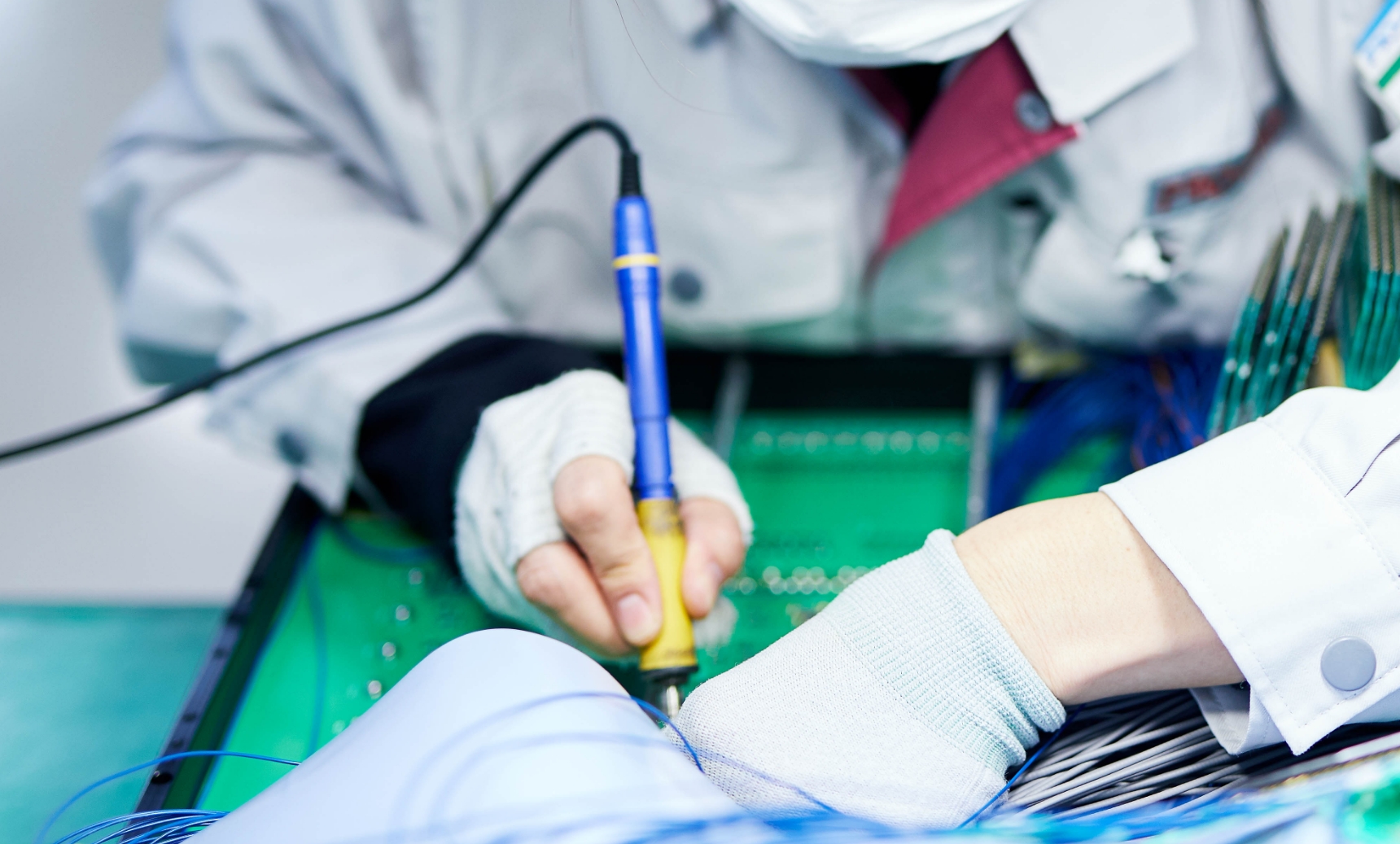
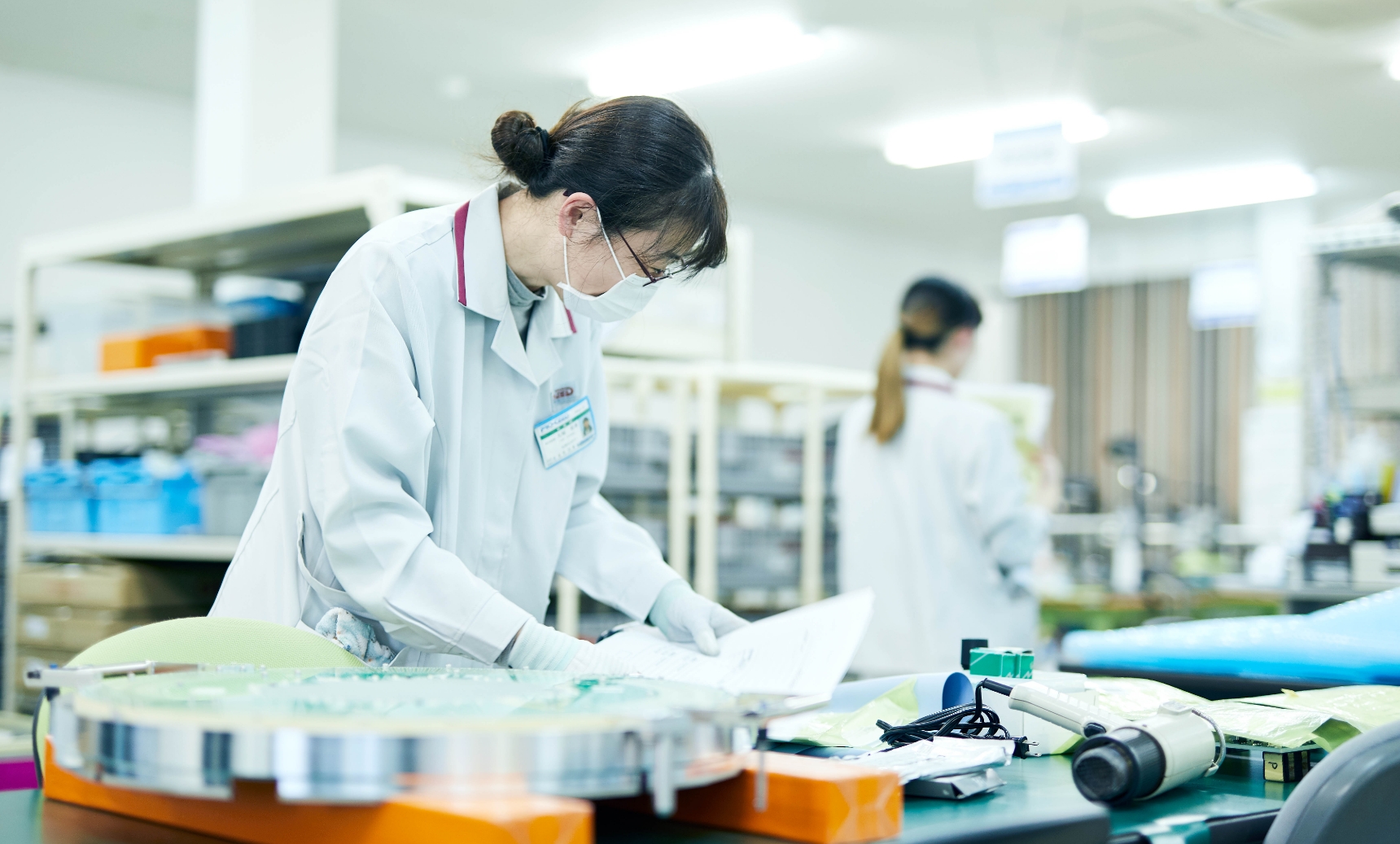
手順2:導通検査
仮組みを終えたマザーボードは、自社開発の検査試験機(PD-1000)を使って導通テストを実行。簡易なリレーのON/OFFによって正しく配線されているかをチェックし、製品の信頼性を高めます。
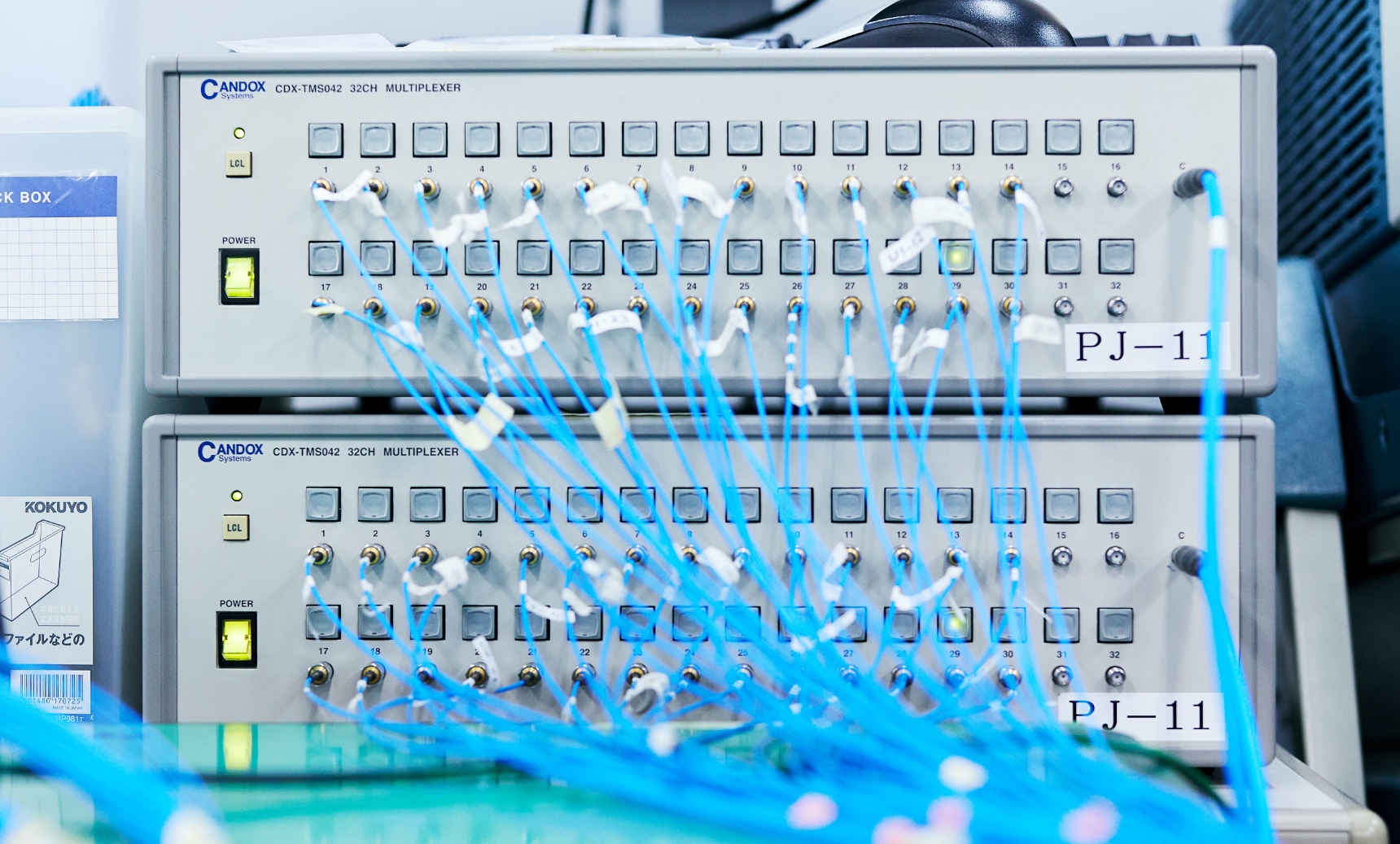
手順3:組立完了
導通検査が完了したら、約4000本ものプローブピンの挿入やケーブル波形試験を行い、外装カバーを取り付けます。最後の調整作業を行えば、半導体試験装置のヘッド部分が完成です。
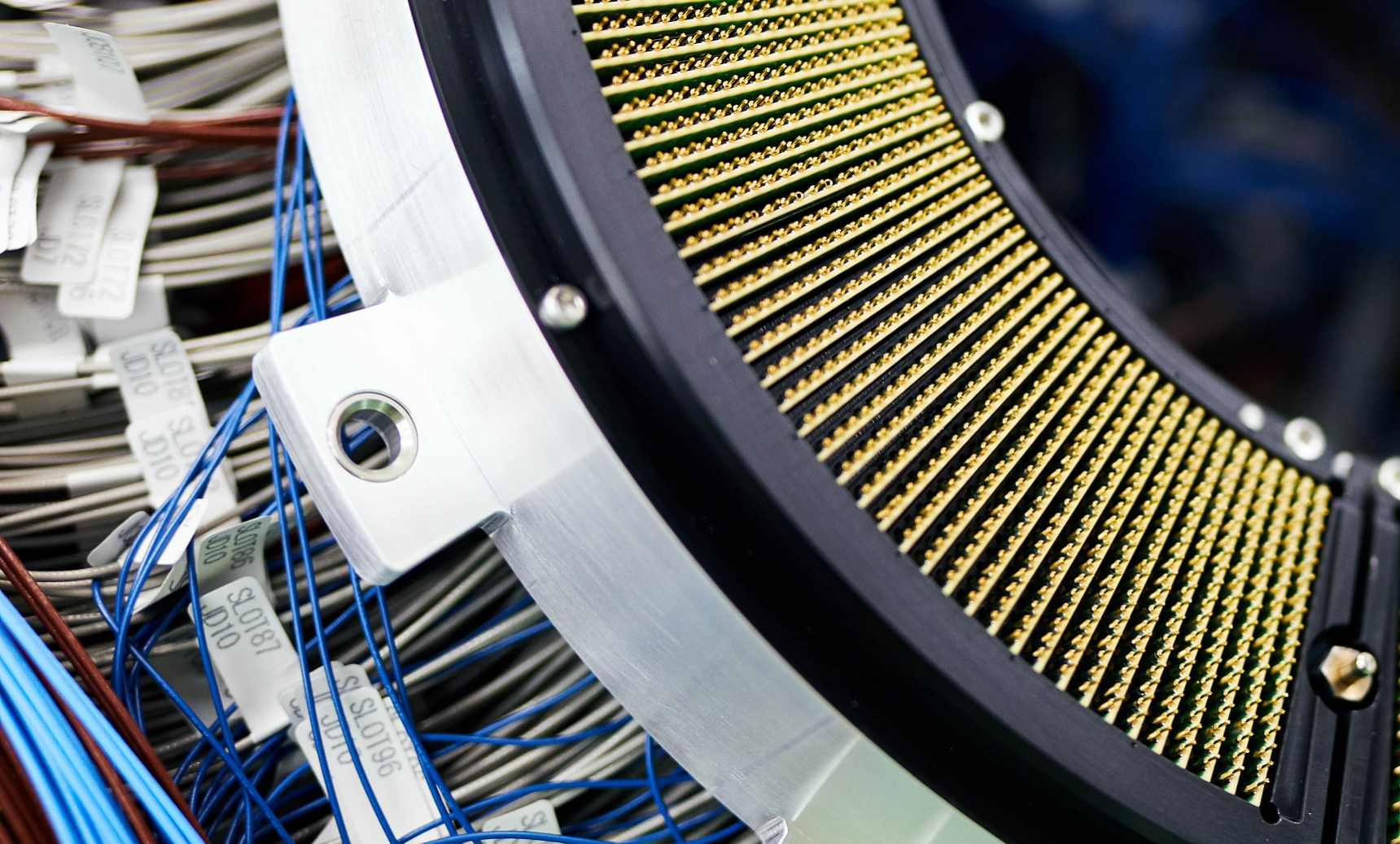
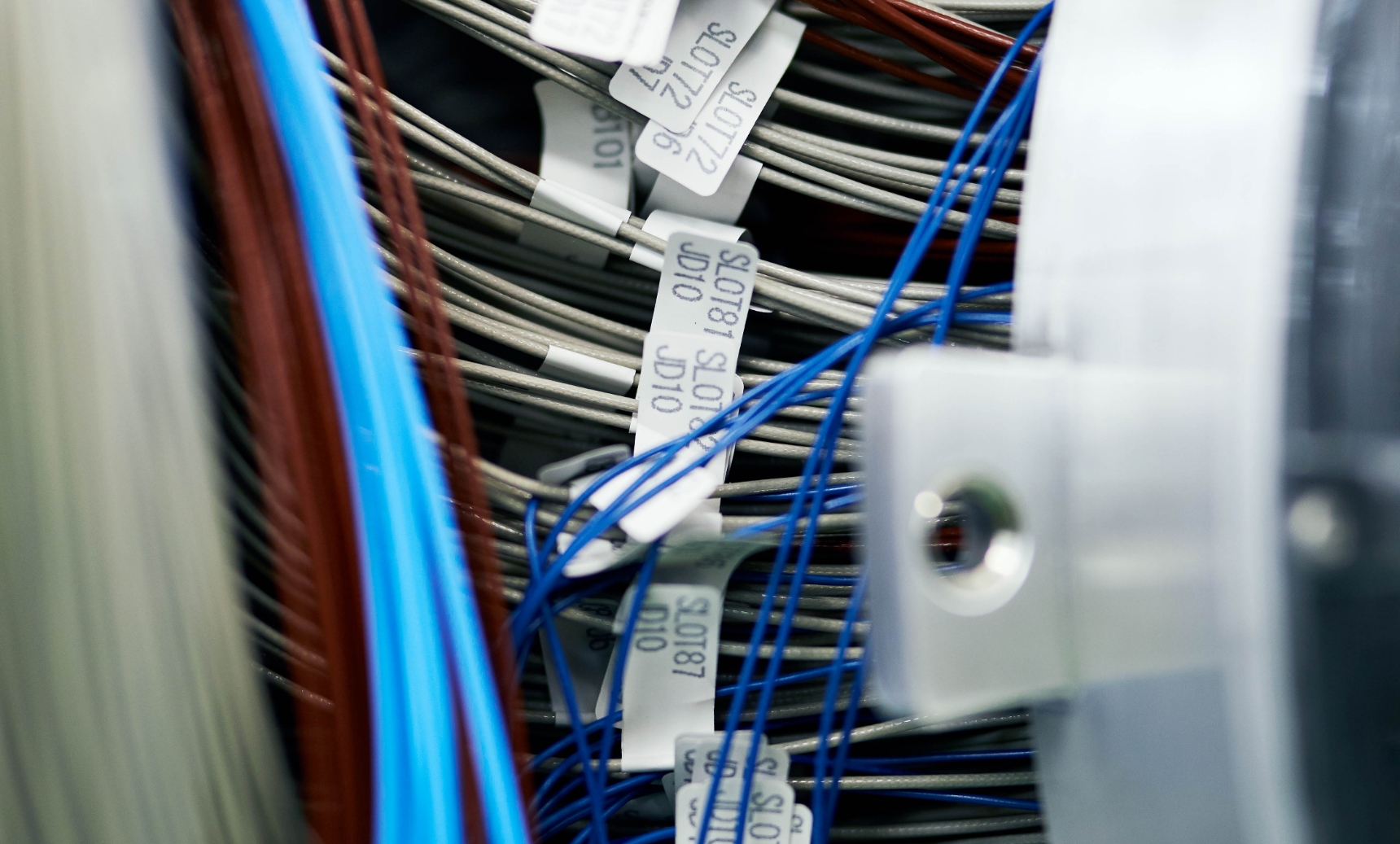
マイクロモジュール
マイクロモジュールの組立・製造
職人にのみ許されるミクロの世界 周波数帯域300KHzから8GHzの高周波計測器類のような、超精密微細部品で構成される製品に対応するべく、プロシードではクリーンルームを完備しています。これにより空気中の微少な浮遊物などの混入を未然に防ぎ、ミクロン単位の精度が求められる作業も可能にしました。もちろんそうした極めて微細な実装が行えるのも、職人的な技術があればこそ。先端設備と熟練技術者の手作業との共働が、「超精密微細部品の実装」「各モジュール間の接続・配線」「金ワイヤーボンディングでの接続」「半導体アッセンブリーの製造」といった高技術&高品質なサービスを実現しているのです。
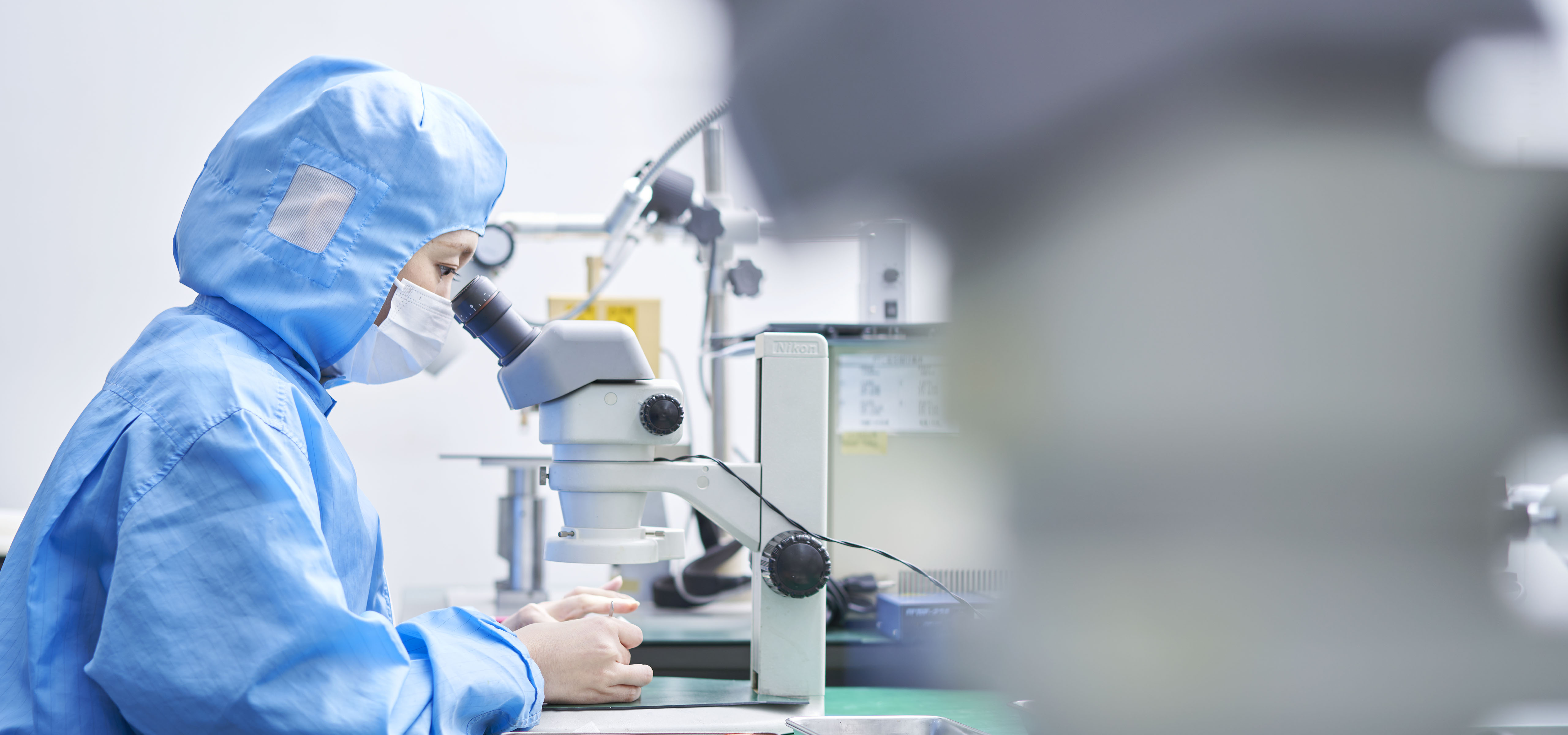
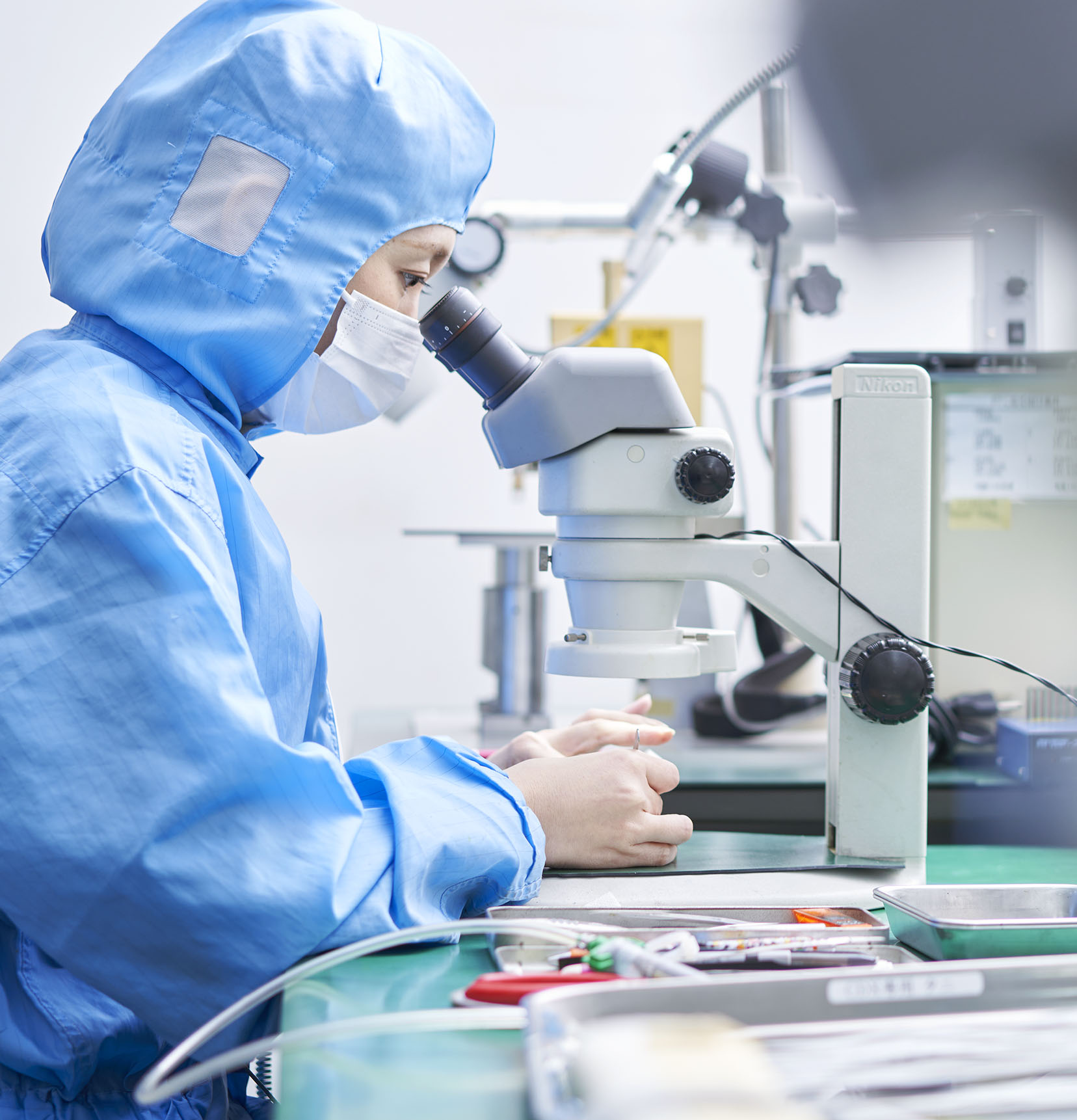
顕微鏡下での実装例をご紹介
熟練の技術を備えた職人だからこそなしえる、超精密微細部品の実装作業。その中でも特に難度の高い「顕微鏡下での接続や配線」について、プロシードが行っている作業の具体例を一部紹介します。
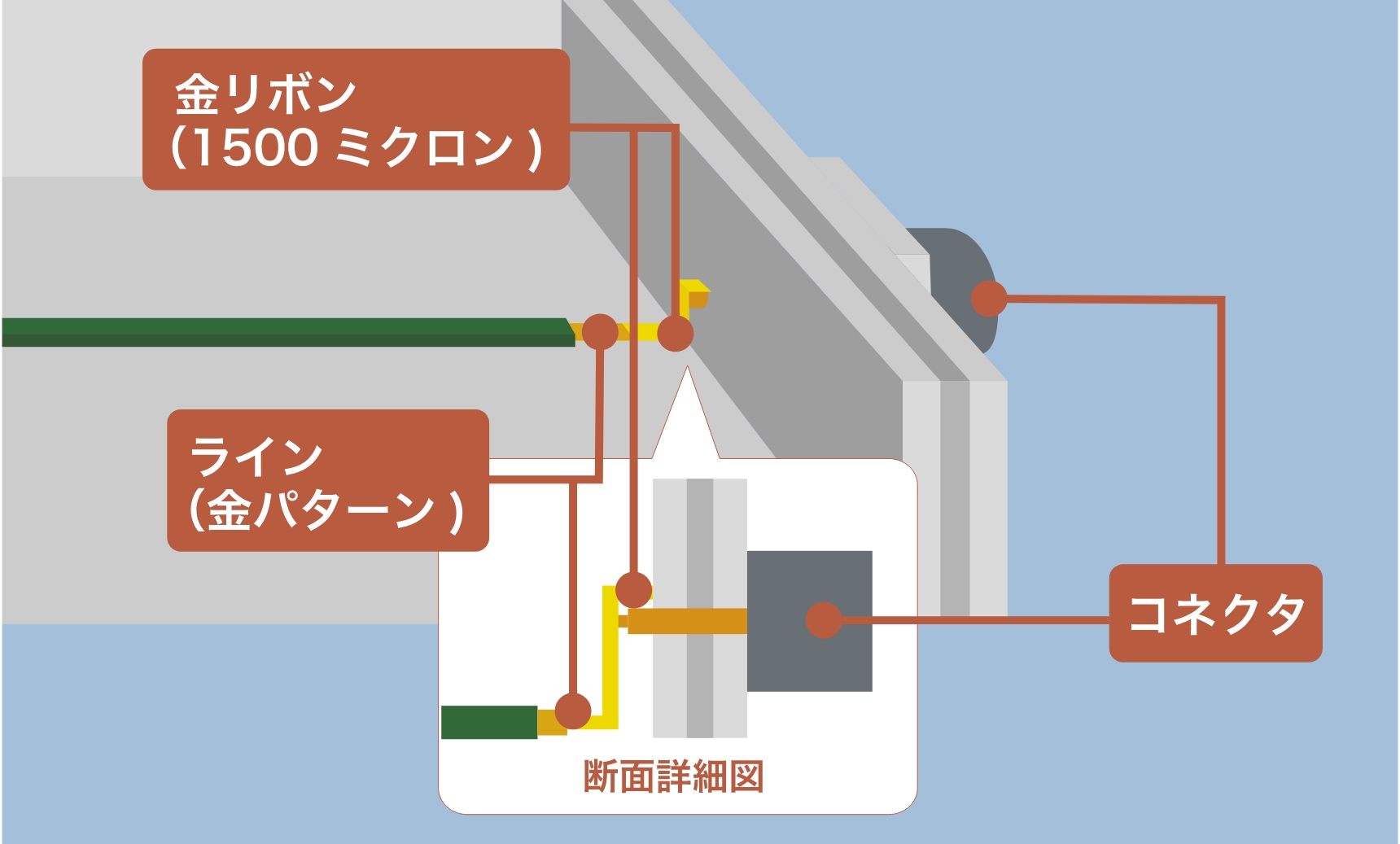
高周波計測器の部品は、性能を確保するために半田付けができません。そこでウエルダーにより板状の金リボンに加重と熱を加え、融着して接続します。
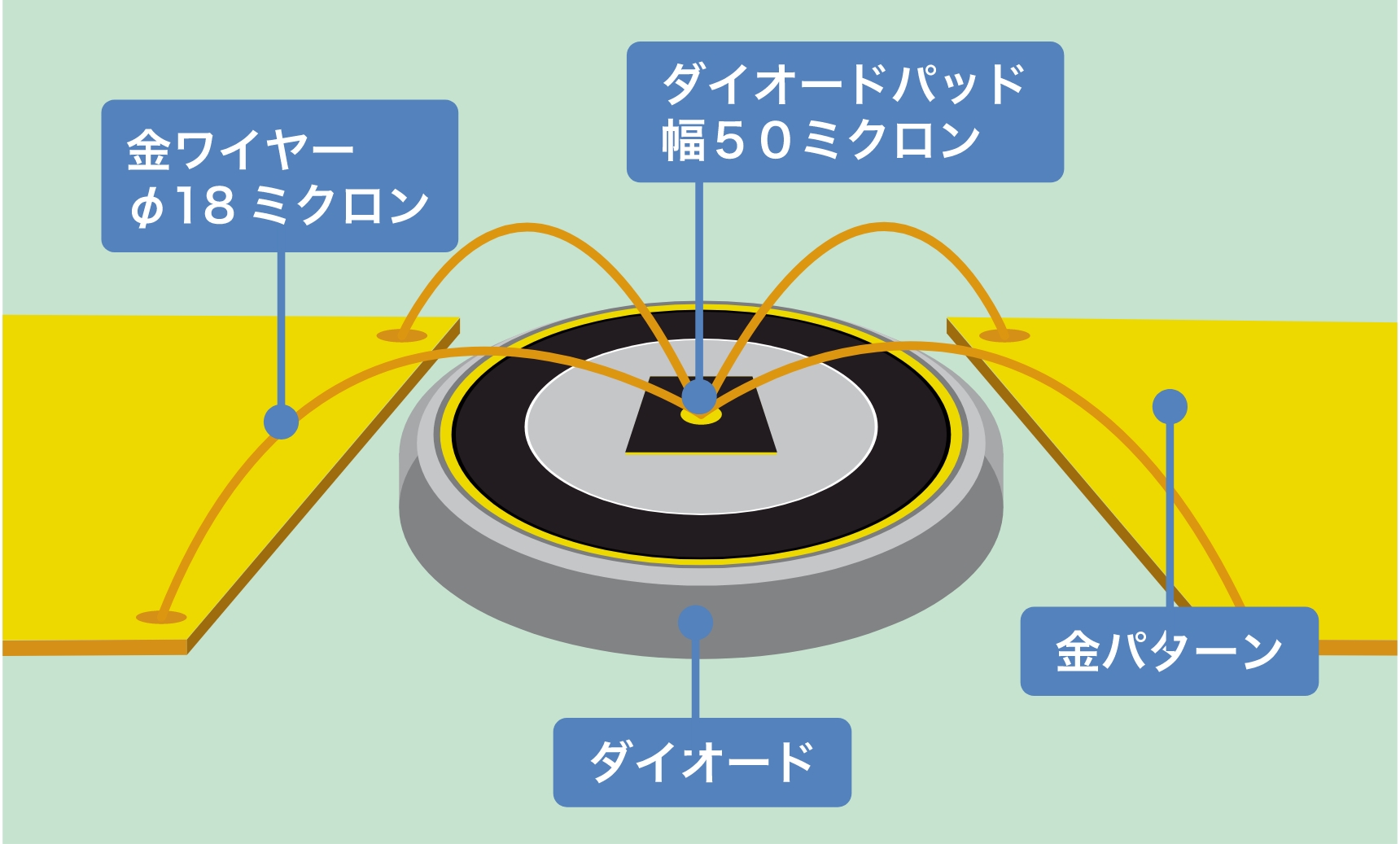
超音波ワイヤーボンダーによって18ミクロンの金ワイヤーに超音波を照射し、わずか50ミクロンの部品パットに融着・接続する超微細な作業です。
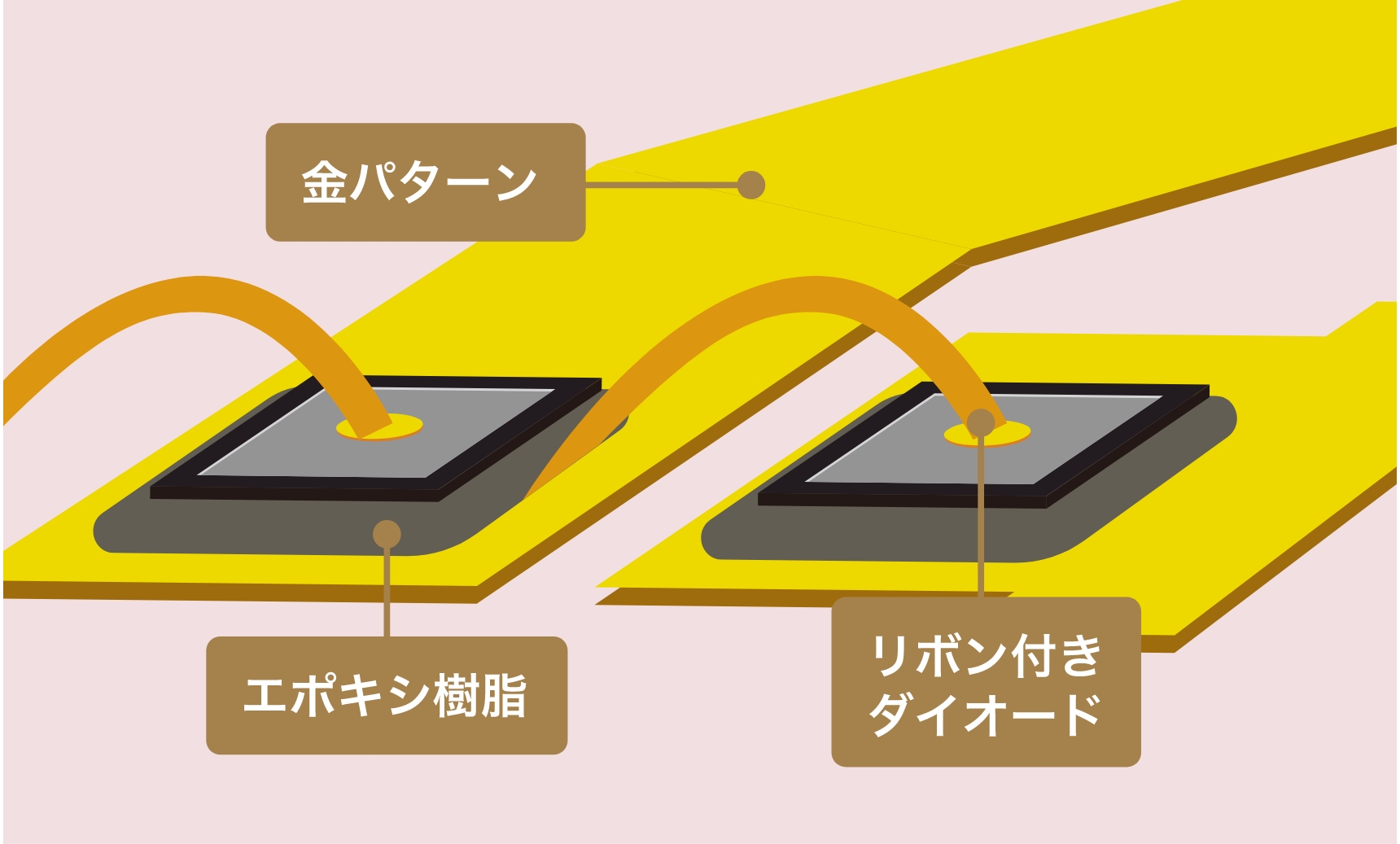
導通したい箇所に導電性エポキシ樹脂を塗布した後、部品を実装。その後、恒温槽で樹脂を硬化させることで導通接合します。
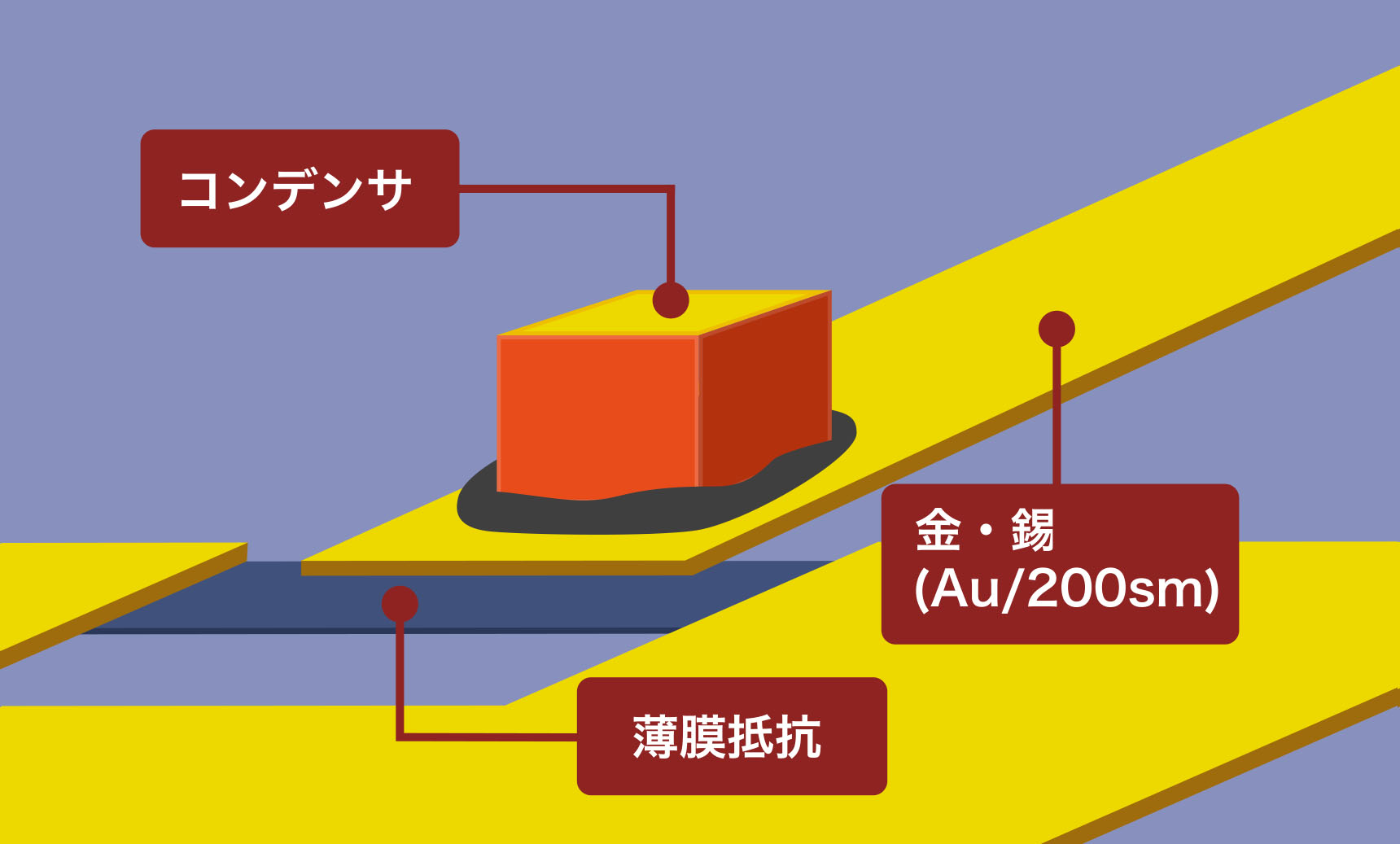
実装面に配置した金錫ペレットを共晶ボンダーで溶かすことで、部品を導通接合します。
システムケーブル
各種ケーブルの製造
多品種・少ロットにも柔軟に対応 産業用電子機器などで使うシステムケーブルの製造でも、職人の技術が光ります。細い同軸線から電源ケーブル用の太い線材まで扱うケーブルは多岐にわたる上、末端に取り付けるコネクタも標準品からヨーロッパ規格品まで様々な部材に対応。1/100mm精度の同軸末端加工装置といった機器設備と、職人の手作業による高精度な加工の合わせ技により、高品質な製品を提供します。もちろん、短納期と低コストの追求もおろそかにはしていません。多品種小ロット生産から少品種大量生産まで、いずれも安心してプロシードにお任せください。
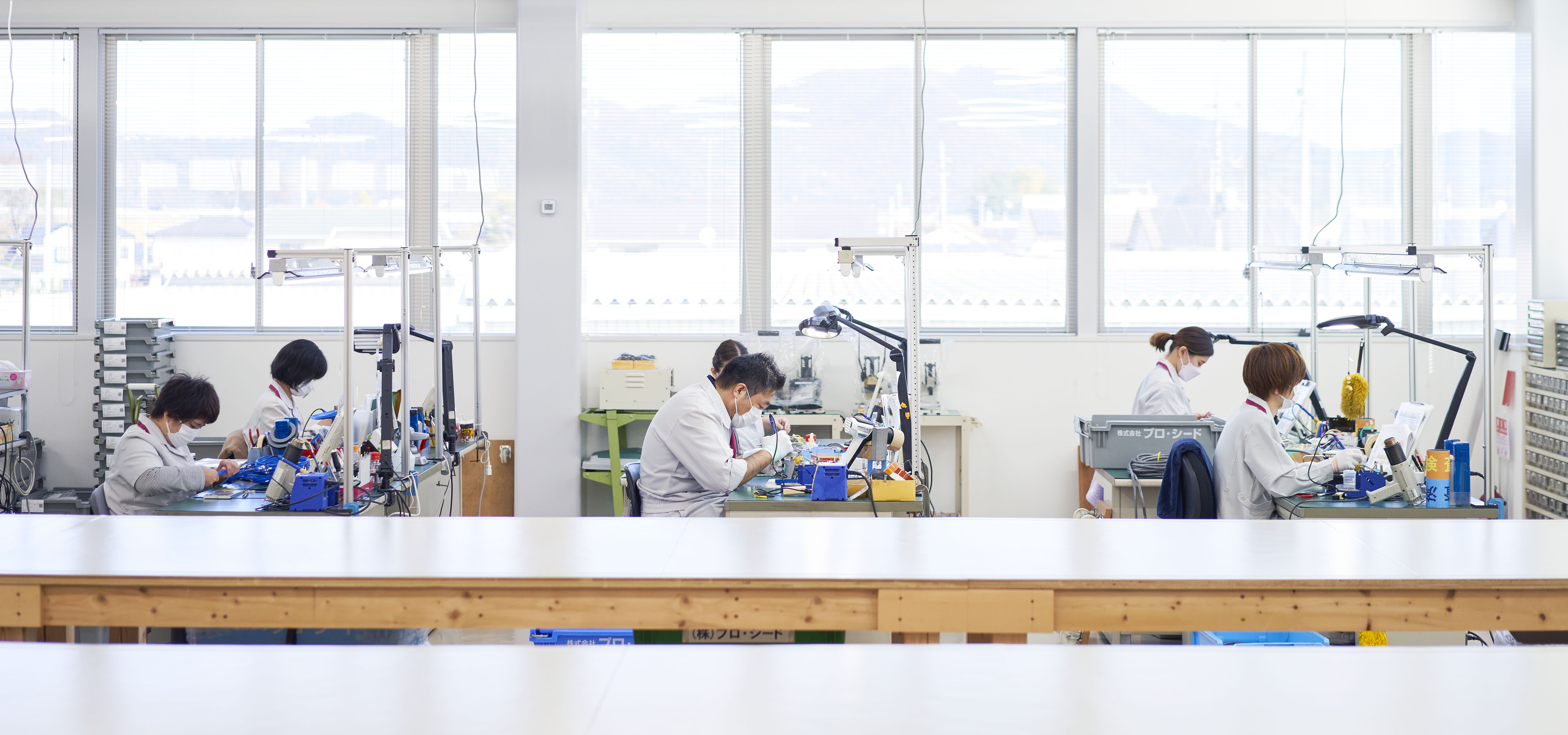
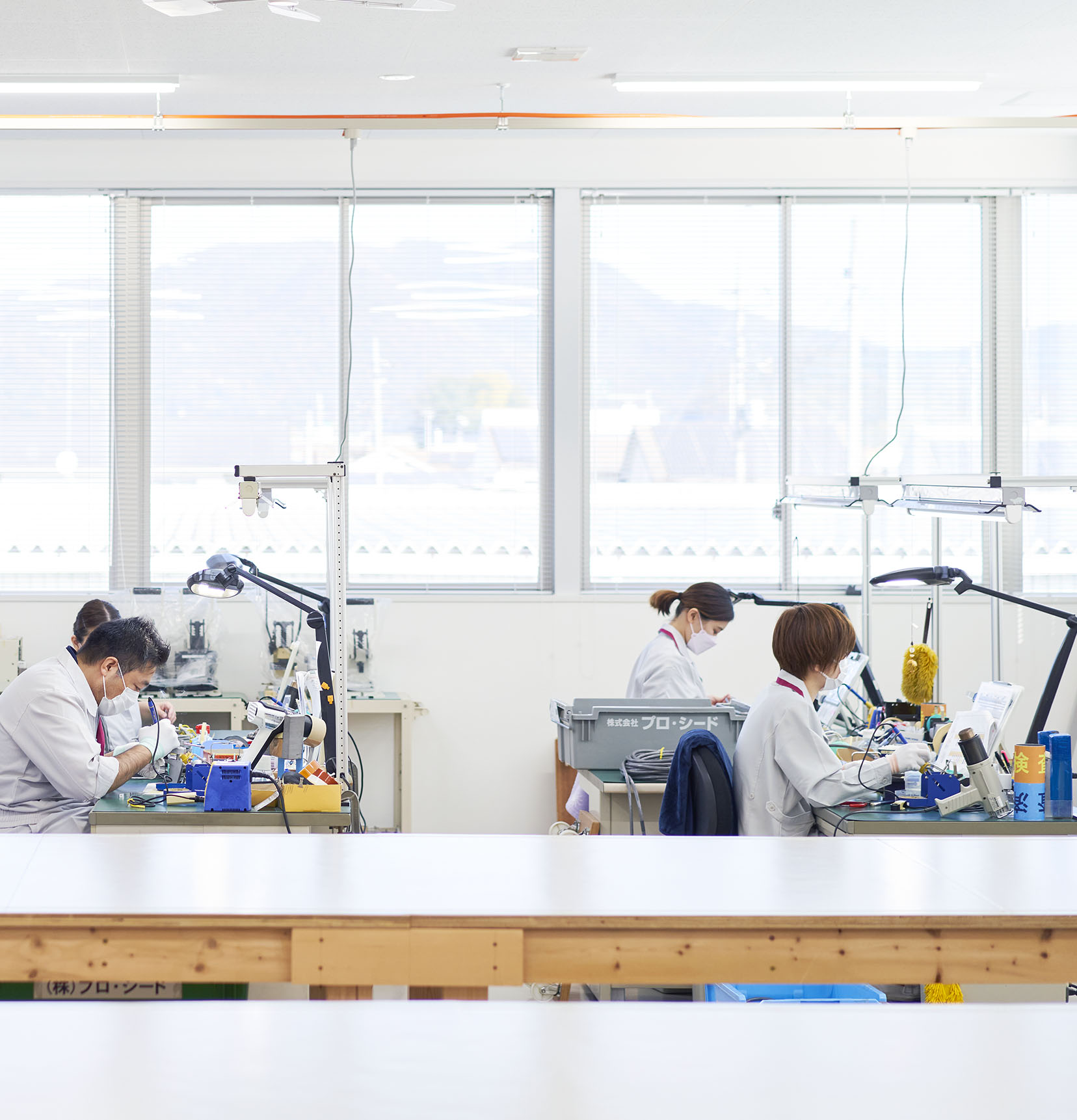
技術力が底上げする
当たり前以上の品質
システムケーブルの加工・製造は比較的シンプルな作業です。しかしだからこそ、技術力の差が顕著に表れるもの。当たり前に思える製品も、実際にご使用いただくことで、プロシードの技術力を確かに実感いただけるはずです。
圧接/圧着/ハンダ作業に対応
圧接、圧着、半田付けといったケーブル両端の加工は、プロシードの技術がわかりやすく発揮されるポイント。特に半田付けでは、コンタクトピッチ1.27mmと#30線(直径約0.3mm)の精密な加工にも対応します。
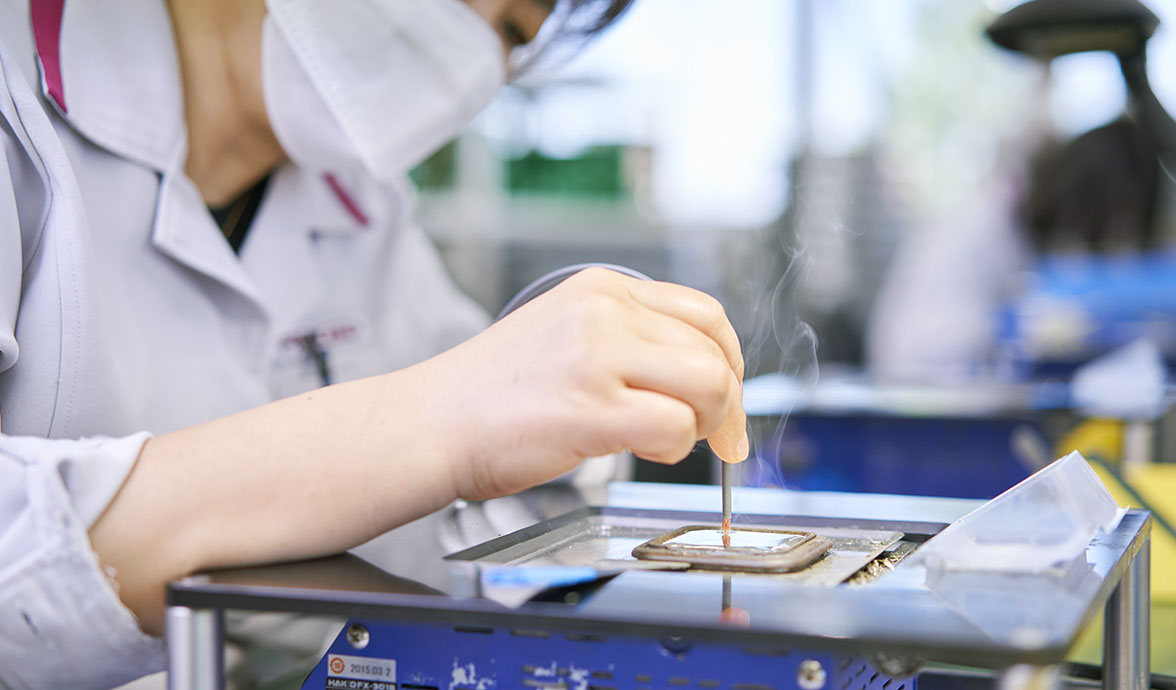
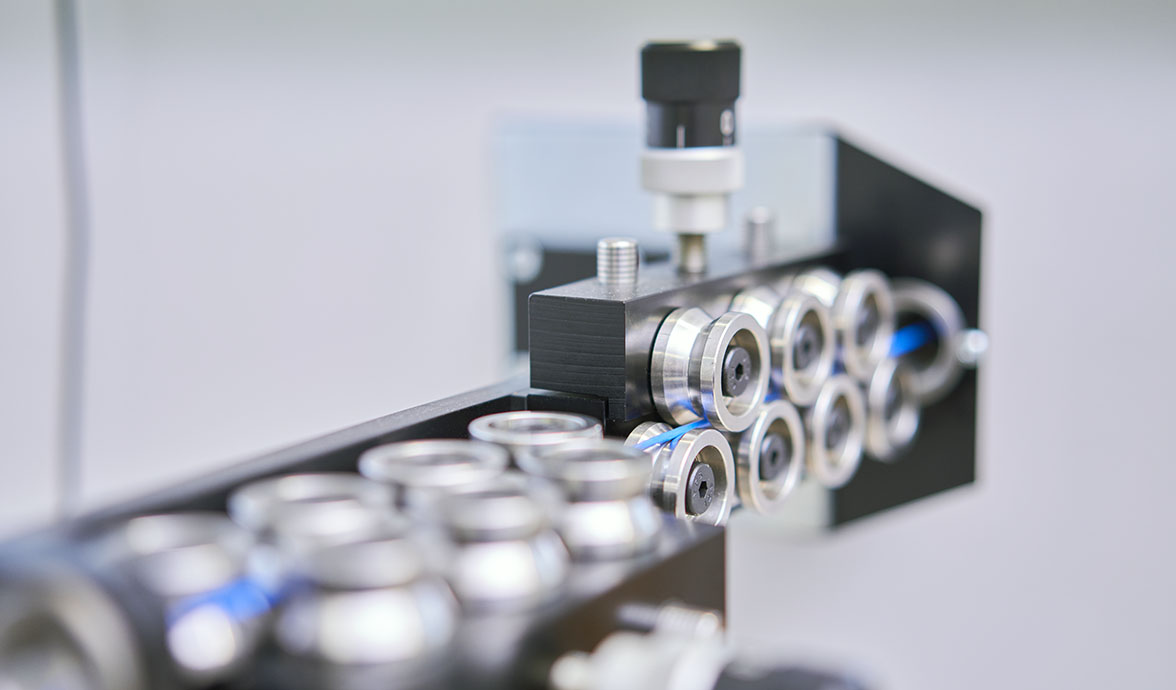
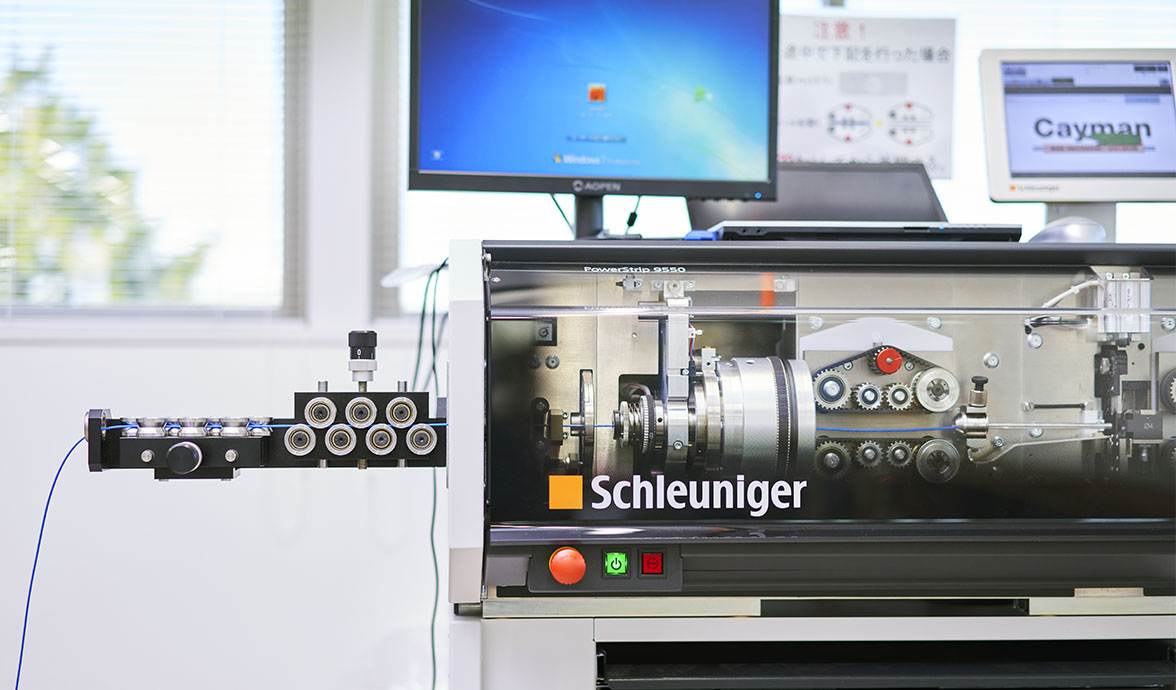
標準品からカスタム品まで製作
支給品はもちろんのこと、自社で購買する多種多様なコネクタ&ケーブルの加工にも対応。量産から多品種少量生産まで、お客様の幅広いニーズに柔軟に応えることが可能です。
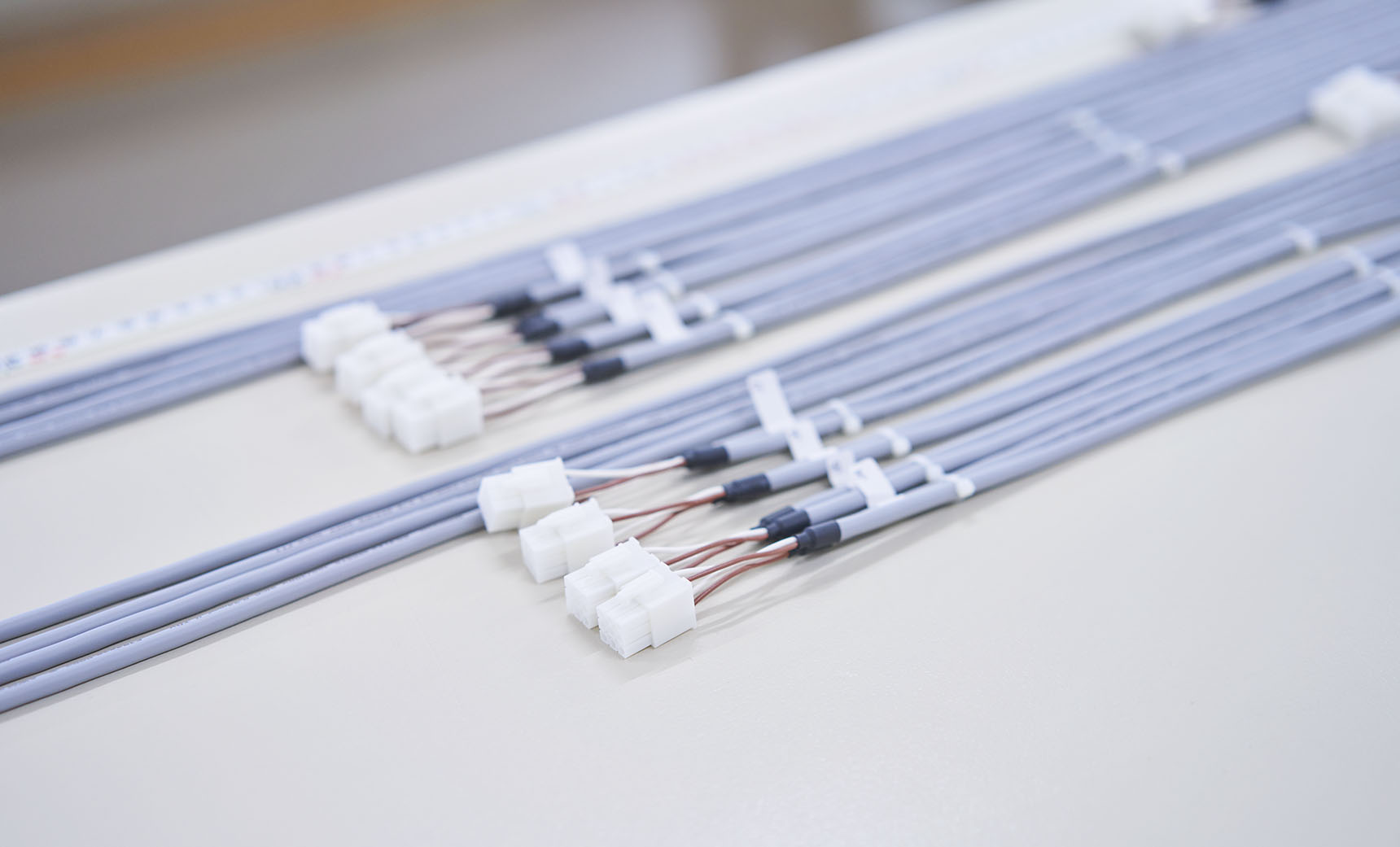
高品質を産む生産体制の最適化
お客様の細かなニーズに応えるために、それぞれ仕様が異なるカスタムケーブル。プロシードでは各ケーブルに最適な生産体制を構築することで、高品質の安定提供に努めています。
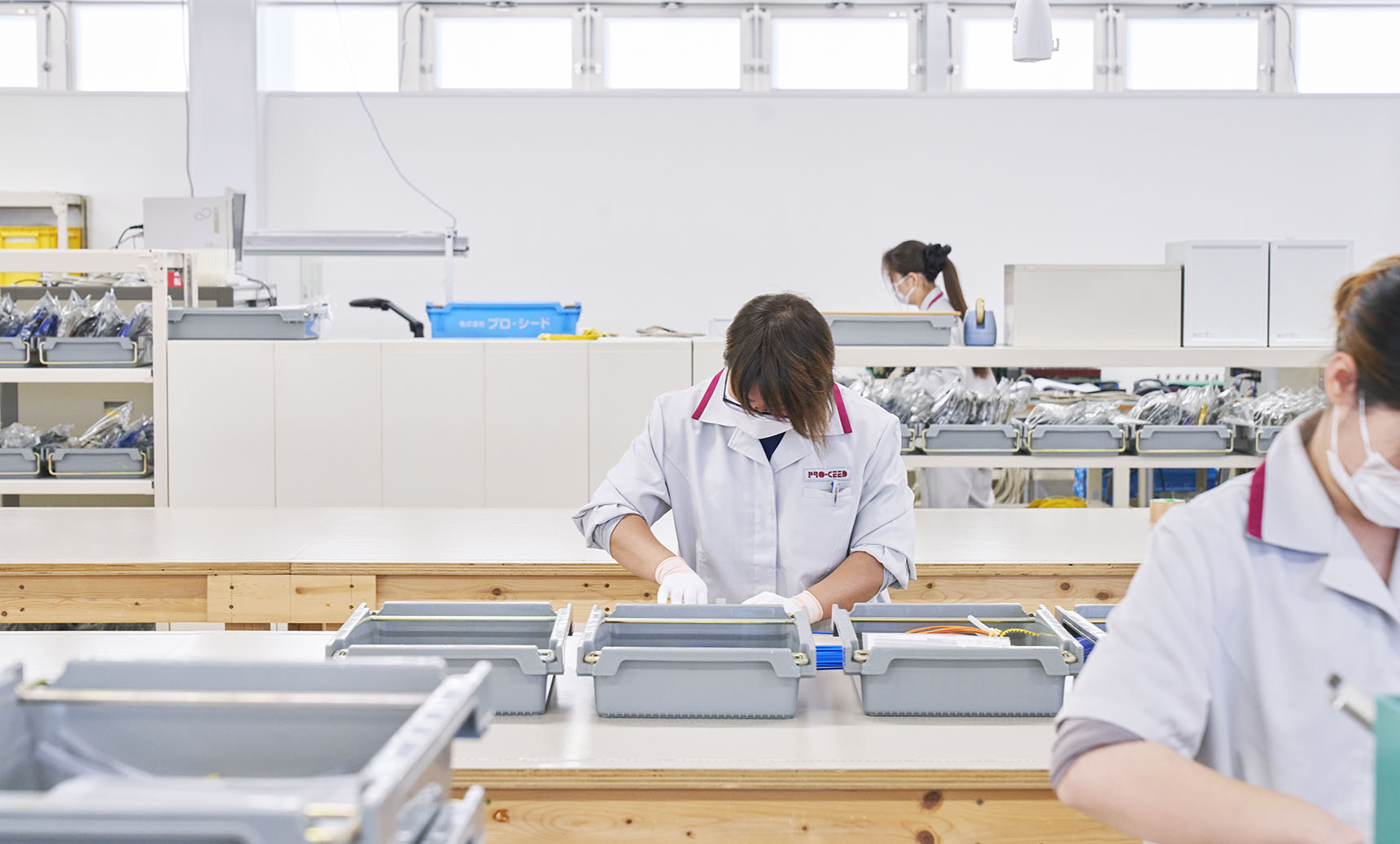
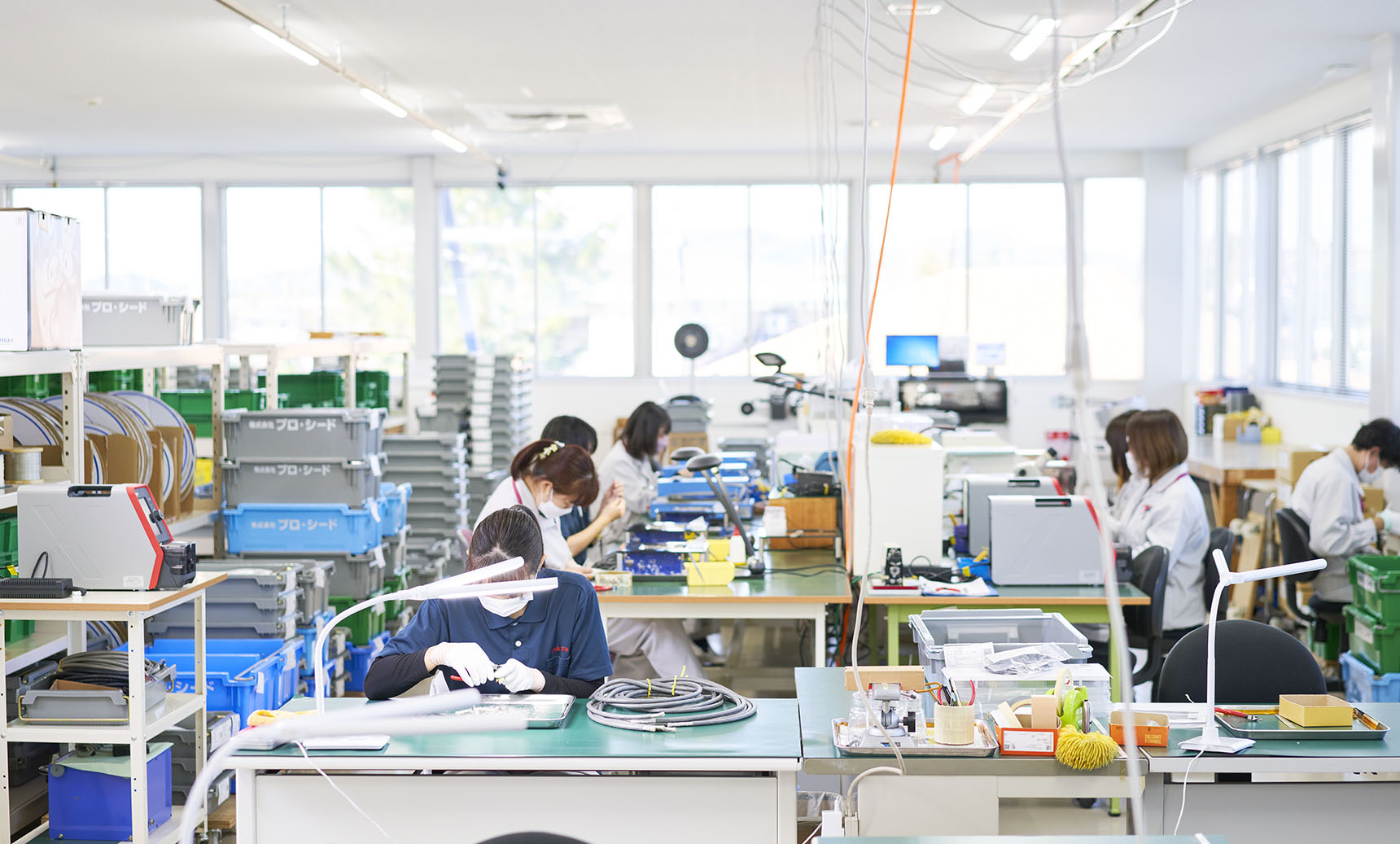